TC17合金是一種綜合性能優良的近β型合金,其名義成分為Ti-5Al-2Sn-2Zr-4Mo-4Cr(質量分數,%),該合金既可在α+β相區進行鍛造也可在β相區進行鍛造。它不但具有較高的強度、淬透性和斷裂韌性,而且耐熱穩定性好,疲勞性能高,熱加工性能好。自上世紀70 年代以來,它以其優異性能逐漸進入航空制造領域,并作為壓氣機盤等鍛件在較高推力的發動機上使用。科研人員通過三種鍛造溫度,研究鍛造溫度對TC17鈦合金低倍組織亮斑的影響。
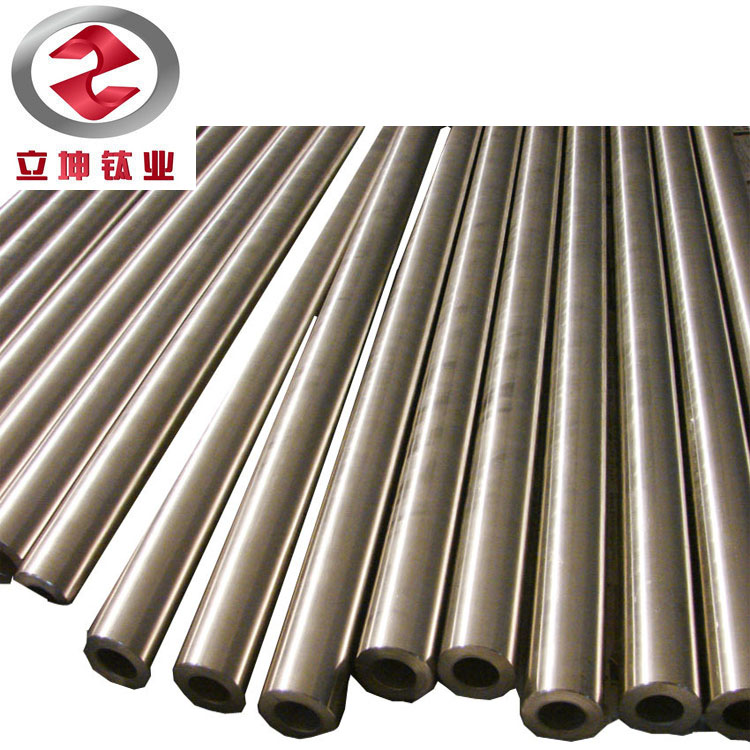
試驗使用Φ140mmTC17鈦合金棒材。棒材顯微組織為β基體上均勻分布等軸α相,α相含量約為50%。實驗用材料由金相法測得該合金的相變點(α+β/β)為880~900℃。
分別在950℃、850℃和830℃的3個溫度下,在2500T快鍛機上對坯料進行60%左右的變形,鍛制成Φ90mm的棒材。對3種鍛造溫度生產的棒材進行低倍組織檢驗,觀察低倍組織亮斑分布情況。在OLYMPUS GX71型金相顯微鏡上進行顯微組織觀察,利用能譜(EDS)分析和顯微硬度測試等手段對亮斑進行分析,并對棒材經840℃/2h.AC+800℃/4h.WC+630℃/8h.AC處理后,檢測棒材的力學性能和金相組織。
鍛造溫度決定著鈦合金的組織及性能,在鈦合金的β相鍛造過程中產生β相變是必然要經歷的相變過程,但若是在兩相鍛造中則β斑為不允許出現的組織缺陷。通過合理的鍛造溫度選擇,可以有效避免β斑產生。
已有的研究表明,β斑點面積越大,對室溫拉伸性能和低周疲勞性能影響越大。美國對Ti-10V-2Fe-3A1合金中β斑點的最大面積規定是0.762mm×0.762mm,俄羅斯對Ti-5553合金中β斑點的最大面積的規定是0.75mm×0.75mm,小于該規定值β斑點對力學性能的影響不大。
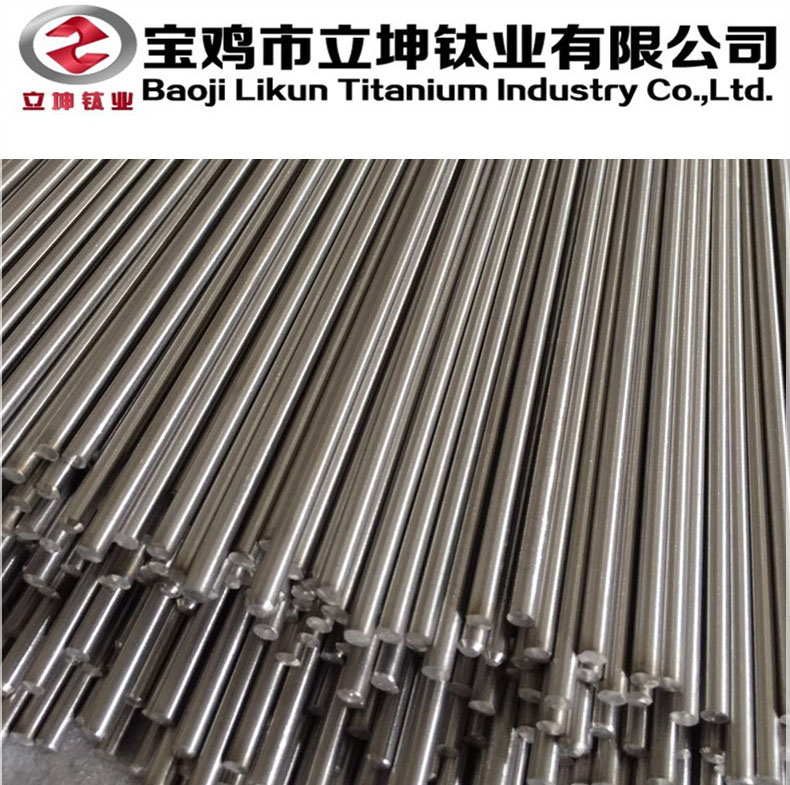
對于近β鍛造的TC17鈦合金產品,應盡量控制變形的均勻性及形變速率,避免局部溫升過大而形成β斑。研究得出以下結論:
(1)微區成分不均勻是引起TC17鈦合金β斑的本質因素,鍛造溫度是形成β斑的主要誘發因素。相變點以下30℃生產,棒材低倍組織中會出現不同程度的β斑。這是因為微區成分分布不均勻,導致該區域的轉變溫度低于基體區,在鍛造中造成局部溫度提前超過相變點,從而形成了β斑。相變點以下50℃生產能有效的避免β斑產生。
(2)研究中所出現的β斑面積約為0.35mm×0.30mm,局部小面積的β斑對TC17鈦合金棒材的整體力學性能未產生較大影響,可以滿足使用要求。
相關鏈接