鈦合金因其優(yōu)異的綜合力學性能、低密度、耐腐蝕、抗疲勞以及顯著的高溫抗拉強度、高溫穩(wěn)定性等,已成為現(xiàn)代宇航、國防工業(yè)關鍵的支撐材料之一。鈦合金的密度只有鋼材
的1/2,但其強度卻高于鋼材(表 1)。正因為鈦合金具有如此優(yōu)異的性能,世界鈦材需求量的 50% 來自航空工業(yè),鈦合金也因此被譽為“空間金屬”,其應用領域分布如圖 1 所示[1] 。在飛機制造業(yè),鈦合金的應用越來越廣泛,尤其在高性能戰(zhàn)斗機的結構件中所占的比重增長幅度非常明顯,如在 F-16 戰(zhàn)機上鈦合金所占重量比僅為 3%,而在作為第 4 代戰(zhàn)機典型代表的 F-22 戰(zhàn)機中所占重量比高達41% [2] 。
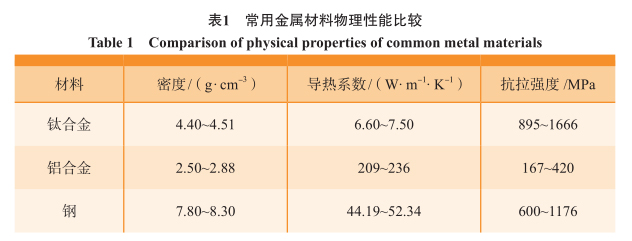
然而鈦合金又是典型的難加工材料,導熱系數(shù)僅為鋼材的 1/7,為鋁合金的 1/30,切削過程刀 - 屑接觸區(qū)極小,單位面積上切削力大且熱量難以排出,切削溫度高,加之鈦合金冷硬現(xiàn)象嚴重,化學活性高,切削狀態(tài)能夠和幾乎所有的刀具材料發(fā)生化學反應,最終導致刀具極易產(chǎn)生磨損破損,鈦合金的高效加工一直是航空工業(yè)面臨的重要制造難題[3] 。鈦合金航空整體結構件大都為壁薄深腔結構(圖 2),材料去除量大,大都在85% 以上,加工周期長,加工過程中回彈現(xiàn)象嚴重,切削顫振現(xiàn)象頻發(fā),更加重了刀具的沖擊載荷,與此同時,加工過程中讓刀誤差與加工變形問題突出,嚴重影響加工質(zhì)量與加工效率的提高。
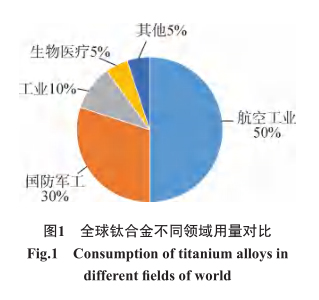
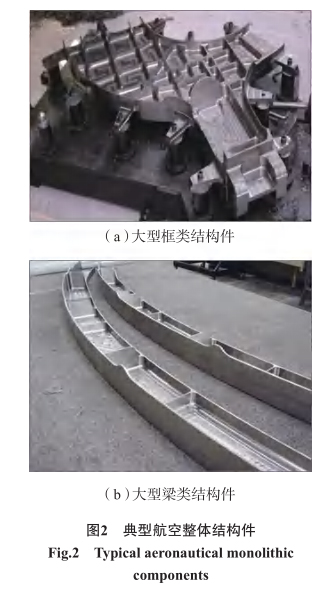
國內(nèi)外學者對鈦合金加工刀具與工藝技術進行了大量理論與試驗研究,有力推動了鈦合金加工質(zhì)量與加工效率的提高。本文對TC11鈦合金切削刀具技術的發(fā)展現(xiàn)狀進行綜述,對加工工藝技術進行分析總結,歸納了制約鈦合金加工性能提升的瓶頸問題,闡明鈦合金切削加工刀具與工藝技術的未來發(fā)展趨勢。
鈦合金加工刀具技術
刀具是實現(xiàn)鈦合金高效高性能加工的關鍵因素,國內(nèi)外學者圍繞鈦合金加工的刀具基體材料、涂層材料以及刀具結構開展了大量的研究工作,取得了諸多創(chuàng)新性的研究成果,促進了鈦合金加工技術的進步。
1、刀具材料與涂層材料
1.1 硬質(zhì)合金刀具材料
硬質(zhì)合金刀具材料加工性能優(yōu)異、性價比高,是目前鈦合金加工的主要刀具材料。硬質(zhì)合金刀具性能與晶粒尺寸密切相關,普通硬質(zhì)合金硬質(zhì)相粒度為幾 μm,細晶粒硬質(zhì)合金平均粒度在 1.0~1.3μm,而超細晶粒硬質(zhì)合金粒度達 0.5μm [4] 。當硬質(zhì)合金的晶粒細化后,硬質(zhì)相尺寸減小,增加了硬質(zhì)相晶粒表面積和晶粒間的結合力,黏結相更均勻地分布
在其周圍,可以提高硬質(zhì)合金的硬度與耐磨性[5] 。數(shù)據(jù)表明,細晶粒硬質(zhì)合金相比較普通硬質(zhì)合金,硬度提高 1.5~2.0HRA,抗彎強度約提高600~800MPa [6] ,而當硬質(zhì)合金中 WC硬質(zhì)相的晶粒尺寸小于 0.5μm,達到超細晶粒水平時,合金的抗彎強度增加 1 倍多(由平均 1600MPa 增加到4000MPa 以上),硬度也明顯增加(由89HRA 增加到大于 93HRA),耐磨性和刀具壽命大幅提高[7] 。因此具備高硬度與高強度“雙高”特性的超細硬質(zhì)合金刀具成為鈦合金這一典型難加工材料加工的首選刀具[8] 。
硬質(zhì)合金刀具的化學成分和黏結相對鈦合金切削性能同樣具有顯著影響,以 WC-TiC 或 TiC 為硬質(zhì)相的硬質(zhì)合金刀具由于與鈦合金親和性較強,切削過程中極易發(fā)生溶解 - 擴散磨損[9] ,因此并不適合于鈦合金切削;而 WC-Co 類硬質(zhì)合金刀具較為適合鈦合金加工[10] 。另外,TaC、NbC、Cr 3 C 2 和 VC 等稀有金屬碳化物的添加可進一步提升超細晶
粒硬質(zhì)合金材料致密度,抑制晶粒異常長大,有效提高刀具高溫硬度與高溫強度,從而降低鈦合金切削過程刀具磨損[11] 。Zhou 等 [12]通過調(diào)整 Co和 Ti 含量制備了不同梯度層厚度和晶粒尺寸的超細梯度硬質(zhì)合金刀具,并通過鈦合金高速切削試驗指出Co10Ti3 基體材料具備更好的切削性能。
總體而言,硬質(zhì)合金刀具由于成本低廉,同時兼具較高硬度與韌性,更多地用于鈦合金中速和低速車削過程以及銑削等斷續(xù)切削過程[13] 。在兼顧效率、刀具壽命等情況下,硬質(zhì)合金刀具用于鈦合金加工時切削速度一般不宜超過 80m/min,當切削速度過高時,高溫導致 Ti、Co 等元素不斷溶解 - 擴散,并伴隨嚴重的黏結磨損與氧化磨損,最終引起刀具材料強度顯著降低,加速刀具失效[14] 。
1.2 刀具涂層材料
涂層硬質(zhì)合金刀具相比無涂層硬質(zhì)合金刀具可顯著降低鈦合金切削過程刀具磨損,提高刀具壽命[15] 。
根據(jù)涂層材料性質(zhì),刀具涂層可分為“硬”涂層與“軟”涂層。“硬”涂層是指具有高的硬度與耐磨性的涂層材料,適用于鈦合金加工刀具的“硬”涂層材料主要有 TiA1N [16-17] 、TiCN [18] 、AlCrN、Ti 6 Al [19] 等,涂層工藝主要有物理氣相沉積法(PVD)、化學氣相沉積法(CVD)等[20] 。“軟”涂層主要指具有低摩擦系數(shù)的涂層材料,涂層本身起到自潤滑作用,如 MoS 2 、WS 2 等,“軟”涂層的制備可采用溶膠 - 凝膠法[21] 。鈦合金加工硬質(zhì)合金刀具涂層結構也經(jīng)歷了從單層到多層[22] 、從普通涂層到元素改性涂層以及納米涂層的發(fā)展[23] 。
用于鈦合金加工的新型刀具“硬”涂層材料不斷涌現(xiàn),Chang 等[24]制備了 CrAlSiN 納米涂層硬質(zhì)合金刀具,涂層硬度可達傳統(tǒng) TiAlN 涂層的 1.3~1.4 倍,在 350m/min 的高切削速度下,CrAlSiN 涂層的刀具壽命達到 TiAlN 涂層刀具壽命的 4.2 倍;肖白軍[25]采用 AlCrN/AlTiSiN 多層納米涂層刀具進行鈦合金切削,刀具壽命是無涂層硬質(zhì)合金刀具的 3.7倍,單涂層刀具的 1.6~2.0 倍。“軟”涂層材料方面,Lian 等[26]將 CrCN-WS 2 硬 / 軟復合涂層沉積在硬質(zhì)合金刀具表面,提高了刀具在干切削鈦合金時的切削性能。涂層結構方面,Oganyan 等[27]比較了無涂層刀具與納米層結構的 Ti-TiN-(Ti, Cr,Al)N 涂層、Zr-ZrN-(Zr, Cr, Al)N涂層刀具的鈦合金銑削性能,得出帶有納米涂層的刀具壽命比無涂層刀具壽命高 2.5~3 倍;Lü 等[28]在硬質(zhì)合金基體上制備了 Si 元素梯度分布的 TiAlSiN 涂層,相比較傳統(tǒng) TiAlN涂層硬度高 147%、附著力提高了300%,并且證明在切削鈦合金時,梯度 TiAlSiN 涂層的刀具壽命比非梯度 TiAlSiN 涂層高 75.4%。
1.3 超硬刀具材料
國內(nèi)外學者一直在探尋超硬刀具材料用于鈦合金加工,立方氮化硼(CBN)、聚晶立方氮化硼(PCBN)以及聚晶金剛石(PCD)等超硬刀具均可用于鈦合金切削[29] 。從物理力
學性能來看,PCD 刀具硬度最高,達 8000HV,是硬質(zhì)合金的 5 倍以上;PCBN 硬度為 3000~5000HV,達到硬質(zhì)合金的 2 倍以上。PCD 刀具導熱性優(yōu)良,導熱系數(shù)達 500W/(m·K)以上,是硬質(zhì)合金的 1.5~9 倍,其數(shù)值也遠高于 PCBN 刀具。PCD 刀具熱膨脹系數(shù)較低,在切削加工中產(chǎn)生的切削熱容易散發(fā),切削溫度較低,刀具不易產(chǎn)生大的熱變形,這一優(yōu)越的特性對于尺寸精度要求極高的精密加工極為重要;PCD 材料還具有較好的化學惰性,在加工過程中鈦合金不容易黏結在刀尖上而形成積屑瘤。CBN 硬度僅次于 PCD,熱穩(wěn)定性極好,在大氣中加熱至 1000℃也不發(fā)生氧化。PCBN 是由 CBN 顆粒和按照一定比例組成的金屬黏結劑或陶瓷黏結劑在高溫高壓條件下燒結而成的,它克服了單晶 CBN 各向異性的缺點[30] 。超硬刀具材料與典型硬質(zhì)合金刀具材料物理力學特性對比如表 2 所示[30-31] 。
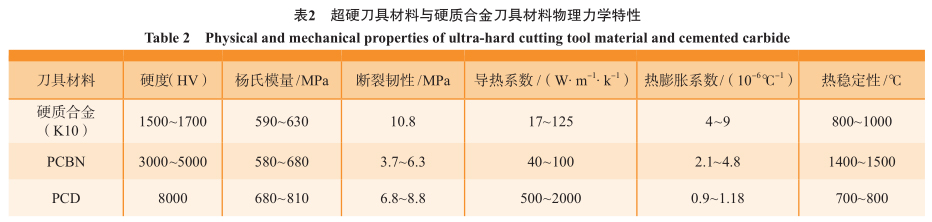
Amin 等[32]的研究表明,當采用1mm 軸向切深、32mm 徑向切深的大去除量切削鈦合金時,PCD 刀具穩(wěn)定切削速度可以達到 120~160m/min。Lindvall [33] 、Ren [34] 等研究了PCD 和 PCBN 刀具高速連續(xù)車削Ti-6Al-4V 合金時的性能和磨損機制,發(fā)現(xiàn) PCD 刀具切削加工鈦合金在刀具壽命方面優(yōu)于 PCBN。
總體而言,涂層硬質(zhì)合金刀具是目前企業(yè)進行航空鈦合金結構件加工的首選刀具,然而鈦合金加工過程刀具損耗嚴重、加工效率偏低、加工成本高的問題依然突出,仍需要硬質(zhì)
合金刀具材料技術與制備技術的不斷進步,從而降低刀具成本,提高加工效率。超硬材料刀具更適合于鈦合金高質(zhì)量加工與高速精密加工,但是超硬刀具材料價格高,工程化應用
受到高昂刀具成本的制約。
2、刀具結構
刀具結構對刀具鈦合金的切削性能和刀具壽命均產(chǎn)生重要影響,隨著刀具設計理論和制造技術的發(fā)展,越來越多的新型刀具結構用于鈦合金加工。
2.1 非對稱分布刀具結構
鈦合金彈性模量低,加工極易產(chǎn)生切削顫振,采用非對稱分布的刀具結構是解決切削顫振問題的有效途徑之一。通過改變刀齒分布形式可以得到非對稱分布結構銑刀,包括變螺旋角銑刀和變齒距銑刀。皇攀凌等[35]設計了變齒距、變螺旋角與變槽深結構刀具,并研究了不同刀具結構加工鈦合金時切削力和振動的變化規(guī)律,其研究結果表明螺旋角39°、齒間角 83°~97°的變齒間角銑刀切削合力與銑削振動較小,最終得到了適用于Ti-6Al-4V鈦合金加工的變齒距立銑刀刀具結構與優(yōu)化的切削參數(shù)。Shaharun 等[36]指出同時具有變螺旋角(48°~53°)與變齒間角(60°~107°)的銑削刀具在切削鈦合金過程中具有更好的減振效果。
非對稱分布刀具結構優(yōu)化的方法主要是通過動力學建模與穩(wěn)定極限圖求解進行切削穩(wěn)定性與刀具結構匹配,最終實現(xiàn)抑振或消除切削顫振,提高加工效率[37] 。
2.2 刀具角度與刃口結構
刀具角度、刀齒分布形式及刃口結構是刀具結構設計中需要考慮的重要因素。多數(shù)研究工作集中于建立刀具角度與切削力及切削振動映射關系,從而實現(xiàn)刀具幾何參數(shù)的優(yōu)化
[38-39] 。刃口結構包括刃口形式與切削刃鈍圓半徑,刃口結構的選擇與加工工況密切相關。劉月萍[40]基于鈦合金切削仿真研究了倒棱刃、消振棱、白刃分別與鈍圓組合的硬質(zhì)合金刀具刃口結構對切削力和溫度的影響,結果表明鈍圓半徑 0.02~0.025mm、倒棱刃寬度 0.06mm 的刃口復合結構可以得到最低切削溫度。Araujo等[41]通過鈦合金銑削試驗研究了刀具刃口半徑與前角對切削力和表面質(zhì)量的影響,給出了優(yōu)化的刀具幾何參數(shù),并指出具有倒棱刃的 PCD 刀片相比較于圓弧刃有更長的刀具壽命。姜振喜
[42]基于 TC4-DT 鈦合金力學性能,設計了具有仿生學原理的特殊槽型和微刃立銑刀,通過抑制切屑鋸齒化,有效地減小了切削力及其波動范圍,降低了硬質(zhì)合金刀具切削振動和切削溫度,得到較小的表面粗糙度,如圖 3 所示[42] 。田汝坤 [43]根據(jù)鈦合金結構件難加工的特點,以前角、后角和螺旋角為因素,利用有限元軟件進行仿真,研究了刀具結構對結構件加工變形的影響并優(yōu)選出適合加工鈦合金結構件的硬質(zhì)合金刀具結構。Zhu 等[44]提出了適用于鈦合金 - 鋁合金疊層材料鉆削的新型多尖刃鉆頭、階梯刃鉆頭以及雙錐角鉆頭,其中雙錐角鉆削刀具與其他刀具相比軸向力更小,平均切削溫度更低,且刀具磨損較小,如圖 4 所示[44] 。
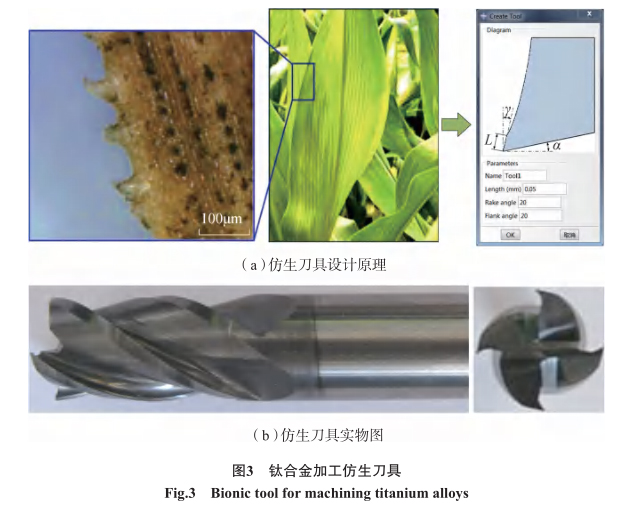
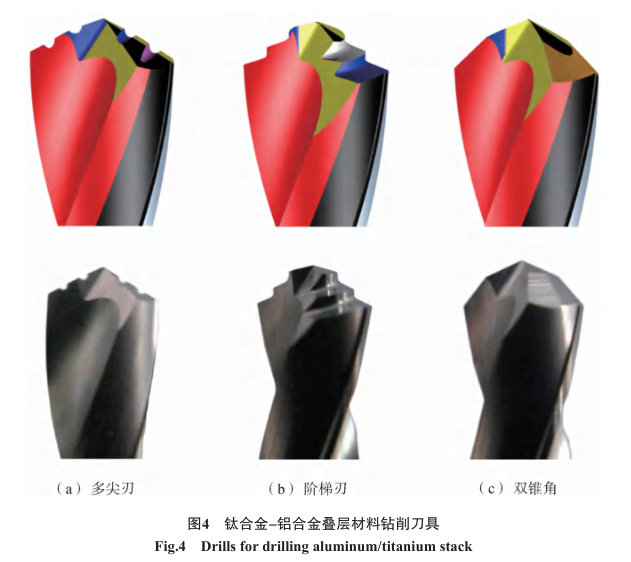
2.3 特定加工需求的刀具
針對輪廓或簡單型腔結構鈦合金加工,山高公司開發(fā)了專用的玉米式銑刀,刀具直徑 D 為 32~80mm,切深可達 0.8D~2D [45] ,實現(xiàn)大切深、大切寬強力銑削,極大地提高了切削效率,降低了切削成本;針對鈦合金結構件狹窄槽腔的幾何特征,山高公司開發(fā)了 JCO710 波紋銑刀,可獲得較長的刀具壽命,適合大軸向切深鈦合金的高效粗加工;三菱材料公司專為鈦合金葉輪葉片的高效精加工而設計了一種新型六刃錐形圓桶球頭銑刀,可以在保持加工表面質(zhì)量的同時實現(xiàn)高效加工;三菱 CoolStar 系列整體立銑刀,將眾多冷卻液孔分布在刀具結構上,最大程度發(fā)揮切削液的冷卻作用,提高加工穩(wěn)定性[46];此外,三菱 VFX 系列玉米銑刀,其外圓周刃可加工側面和臺階面的立面,底刃可加工平面,大幅提高了切削用量和加工效率,切削速度可達 55m/min,進給量0.12mm/tooth,徑向切深 10~45mm,軸 向 切 深 25~60mm,以 直 徑 為63mm 為例,最大金屬去除量可達
400cm 3 /min [47] ;Helical 公司研發(fā)了適用于鈦合金加工的 HXF 系列多齒硬質(zhì)合金刀具,齒數(shù)達 7~14 齒,通過增加刀齒數(shù),減小每個刀齒切削載荷的同時有效提高切削效率。上述鈦合金加工專用刀具如圖5所示。
1.3 刀具深冷處理技術
研究表明,切 削 刀 具 在 -80~-196℃的低溫下進行深冷處理 24~40h,可以改善刀具切削性能,提高刀具壽命[48] 。Strano 等 [49]通過試驗研究了 -196℃液氮低溫處理的涂層硬質(zhì)合金刀具切削性能,發(fā)現(xiàn)經(jīng)過低溫處理的刀具基體與涂層材料硬度分別增加 7% 與 11%,當切削鈦合金速度在 62~79m/min 時,刀具壽命可以提高 9%~30%。Sivalingam 等[50]研究了 TiAlN/NbN 涂層硬質(zhì)合金刀片在 24h 與 48h 液氮深冷處理后的鈦合金銑削過程中刀具磨損過程,與未經(jīng)深冷處理的刀片相比,在經(jīng)過 48h和 24h 低溫處理的刀片磨損分別降低了 12%~23% 和 4%~11%,并同時觀察到了切削力和切削振動的降低。
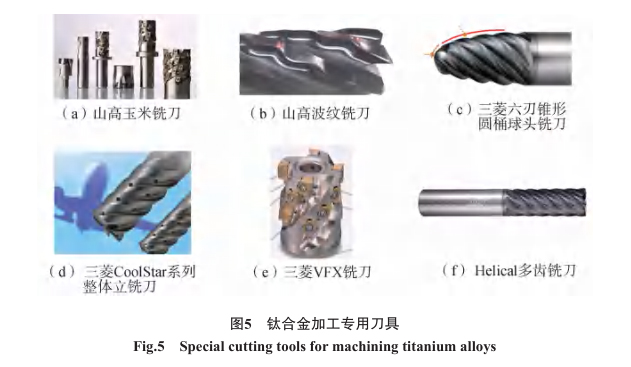
綜合結果表明,在相同的工作條件下,深冷處理刀具具有更好的加工性能和更長的刀具壽命。
鈦合金加工工藝技術
1、鈦合金加工工藝優(yōu)化
目前鈦合金的切削加工工藝主要以車削、銑削和鉆削為主,航空鈦合金結構件加工以銑削為主。車削加工時切削溫度較高,刀具壽命低,大部分的研究致力于選用合適的切削液和工藝參數(shù)降低切削溫度。鈦合金銑削加工時,由于加工過程中循環(huán)熱力載荷的作用,使得切屑與刀刃容易黏結,刀具磨損嚴重,大部分的研究通過工藝參數(shù)優(yōu)化減小刀具磨損,提高加工表面質(zhì)量。鉆削加工時容易導致鉆頭燒結、卡鉆甚至折斷等問題,鉆孔質(zhì)量差,多采用超聲輔助、改善加工環(huán)境等方法提高鈦合金鉆削的切削加工性。因此,合理的加工
參數(shù)選擇對保證鈦合金加工質(zhì)量、降低加工成本、提高生產(chǎn)效率具有重要意義。
常見的切削加工參數(shù)優(yōu)化方法大多基于田口法[51-52] 、響應曲面法 [53]等設計試驗,以減小實際試驗組數(shù),通過不同的分析方法,如方差分析、回歸分析法、神經(jīng)網(wǎng)絡法、遺傳算法、蟻群優(yōu)化、粒子群優(yōu)化算法等,建立單、多因變量的預測模型,實現(xiàn)單一或多目標的加工參數(shù)優(yōu)化,獲取最佳工藝參數(shù)組合。Jiang 等[54]通過正交試驗研究了干切削、潤滑液切削與微量潤滑(Minimum quantity lubrication,MQL)切削等不同冷卻潤滑條件下切削參數(shù)對鈦合金銑削表面粗糙度的影響,并通過多項式回歸擬合指出表面粗糙度值 R a 對每齒進給量和軸向切深更敏感,相比較來說,R a 對切削速度和徑向切削深度不敏感。Gupta 等[55]應用響應曲面法和粒子群優(yōu)化技術,在 MQL 環(huán)境下,對鈦合金切削工藝參數(shù)進行多響應優(yōu)化。另外,可以借助切削仿真進行工藝優(yōu)化,建立切削過程有限元模型并對加工參數(shù)的選取提供指導[56] ,既節(jié)省了試驗成本又能實現(xiàn)相應目標的優(yōu)化分析。
通過目前的研究可以看出,在切削加工參數(shù)優(yōu)化中,優(yōu)化分析大都以單一目標提出最優(yōu)加工參數(shù)方案,但從機械產(chǎn)品質(zhì)量、刀具壽命、生產(chǎn)成本等多目標出發(fā)的優(yōu)化參數(shù)方案獲
取方面的研究還存在一定的局限性。
2、鈦合金綠色加工技術
由于鈦合金的難加工性,傳統(tǒng)的鈦合金切削加工需應用大量的切削液,環(huán)境污染嚴重,能源消耗較大。綠色高效切削加工鈦合金工藝受到越來越多的關注。目前國內(nèi)外常用的鈦合金綠色加工工藝可分為綠色冷卻技術和綠色潤滑技術。其中綠色冷卻技術有低溫輔助冷卻切削(液氮、CO 2 )[57] 、低溫空冷切削 [58] 、高壓冷卻切削[59-60]等。研究表明,
與干切削和切削液切削相比,利用液氮和 CO 2 進行低溫冷卻輔助切削可將切削溫度分別降低 50% 和15%~47% [61] ,同時在試驗條件下刀具壽命可提高 16%~100% [62-63] ,表面粗糙度可降低 31%~39% [64] 。高壓冷卻切削主要是在切削液噴射過程中加入壓力,提高對流換熱系數(shù)從而降低切削溫度,與干切削相比,可提高刀具壽命 55%~60% [60] 。Jamil 等[65]通過 CO 2 -snow 與液氮冷卻的鈦合金車削試驗發(fā)現(xiàn),相比較于液氮冷卻,CO 2 -snow 具有更好的冷卻效果,刀具磨損、切削力、表面粗糙度總體更小。
綠色潤滑技術有噴霧射流潤滑(Atomization-based cutting fluid,ACF)[66] 、MQL [67-69] 、水蒸氣冷卻潤滑[70]等。噴霧射流技術是利用高速氣體將潤滑液分散成均勻大小的液滴,形成聚焦的射流進入刀屑接觸區(qū),實現(xiàn)冷卻潤滑的效果。研究表明,噴霧射流技術應用于鈦合金切削中可有效提高刀具壽命[71] 。MQL 技術能在最小切削液用量的條件下實現(xiàn)最大潤滑效果,該技術利用高壓將少量切削液噴射至切削區(qū)域,在降低切削溫度的同時實現(xiàn)較好的潤滑效果,從而達到可持續(xù)、低成本切削的目的[72] 。水蒸氣冷卻潤滑是通過水蒸氣與金屬表面發(fā)生化學反應,形成的多維金屬氧化邊界潤滑層,增加了潤滑效果,從而降低切削力、提高刀具壽命[73] 。Jamil 等 [74]提出采用乙醇 - 脂類油 - 干冰混合進行冷卻潤滑可以降低切削過程摩擦力。
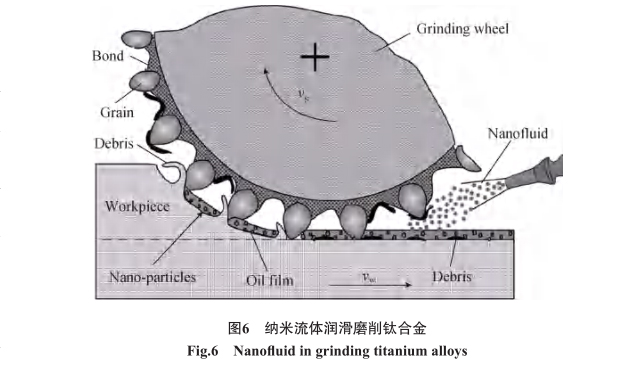
近 年 來,研 究 人 員 將 納 米 顆粒混合在冷卻介質(zhì)中,借助納米顆粒的高導熱性和潤滑性提高切削加工中的冷卻和潤滑效果,從而降低切削溫度和切削力,減少刀具磨損,以此提出一系列新的冷卻潤滑技術。納米顆粒包括 SiO 2 、SiC、碳 納 米 管(CNTs) 、Al 2 O 3 [75] 、石 墨 烯[76] 、氧 化 石 墨 烯 [77-78] 、石墨等[79] 。Li 等 [76]將石墨烯混合在植物油中進行鈦合金銑削,通過對切削力、切削溫度和表面完整性等銑削特性的對比,得出石墨烯添加劑可以提高銑削區(qū)油膜的冷卻和潤滑性能,能有效改善材料的銑削性能。Yi等[78]在鈦合金鉆削加工中將氧化石墨烯混合于切削液中,有效地改善了切削液的潤滑作用,獲得了更好的鉆孔表面,切削力減小了 17.21%。將納米顆粒流體與 MQL 技術相結合,并通過參數(shù)優(yōu)化,能夠充分發(fā)揮納米顆粒的導熱與潤滑作用[80-81] ,如圖 6所示[80] 。Bai 等 [75]以花生油為基體進行了鈦合金銑削試驗,探索 6 種不同的納米流體(Al 2 O 3 、SiO 2 、MoS 2 、CNTs、SiC、石墨)對鈦合金加工的影響,得出 Al 2 O 3 和 SiO 2 納米流體對切削液的潤滑作用提高最多。此外,Singh 等[82]將 Ranque-Hilsch 渦流管引入 MQL 冷卻系統(tǒng),通過純鈦切削加工證明了相比于傳統(tǒng) MQL 具有降低刀具磨損的效果。
由于鈦合金綠色加工技術涉及傳熱學、摩擦學、流體力學等多學科的交叉融合,目前鈦合金綠色加工技術的研究多停留在試驗階段,其具體的綠色加工機理的研究較少。因此
需要深入分析切削液與刀具、工件、切屑間的冷卻、潤滑作用機理,提出針對不同需求的綠色加工工藝,實現(xiàn)鈦合金綠色高效加工。
鈦合金結構件切削加工顫振
1、鈦合金結構件切削加工顫振分析與穩(wěn)定性預測
TC11鈦合金結構件弱剛性特征導致加工顫振問題尤為突出,加工過程顫振分析與穩(wěn)定性預測引起學術界與工程界的廣泛關注。Ma é 等[83]通過主軸組件速度相關的動態(tài)行為建模研究,建立了考慮主軸 - 刀具 - 薄壁工件動態(tài)特性的動力學模型,并驗證了其在銑削穩(wěn)定性預測中的正確性。梁睿君等[84]針對弱剛性薄壁零件頻響特點與高階動態(tài)特性,研究了
多自由度銑削動力學建模方法并提出無顫振穩(wěn)定切削參數(shù)閾值。Wang等[85]針對薄壁件銑削過程時變動態(tài)特征與多模態(tài)耦合特征提出一種多模態(tài)動力學建模方法,從而進行銑削
穩(wěn)定性預測。
目前鈦合金結構件切削加工顫振分析與穩(wěn)定性預測研究工作主要分為兩方面,一方面集中在發(fā)展傳統(tǒng)穩(wěn)定性極限圖模型,從二維向多維演變;另一方面,充分考慮薄壁結構切削過程時變動力學特性與非線性特性并集成在動力學建模中,以提升顫振穩(wěn)定性預測精度[86] 。
2、鈦合金結構件切削加工顫振抑制
鈦合金結構件切削顫振抑制主要包括增強系統(tǒng)剛度特性、阻尼特性和工藝優(yōu)化等。
(1)增加切削系統(tǒng)的剛度或者阻尼。
Kolluru 等[87]提出將分散的質(zhì)量體作為粘彈性層附置于大型薄壁零件上,這種表面阻尼方法可以有效地抑制這一工況的加工振動(圖7)。Wan 等[88]提出在薄壁件上附加質(zhì)量塊,并通過數(shù)值計算附加質(zhì)量塊的工件模型模態(tài)參數(shù),結合計算結果進行質(zhì)量分布優(yōu)化,最終提高薄壁件切削穩(wěn)定性(圖 8)。Yang 等[89]通過將單自由度被動阻尼器集成在銑刀內(nèi)部,設計了一種適用于加工深腔和深孔特征的阻尼銑刀,并通過試驗證明了阻尼銑刀在長徑比為 8 的情況下可以減小 75% 的切削振幅。
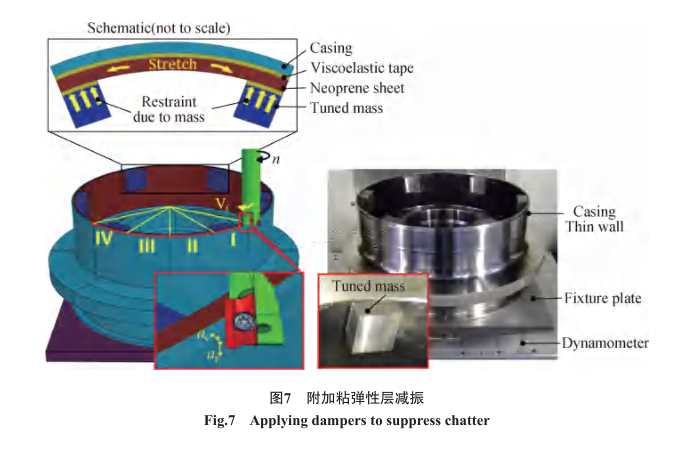
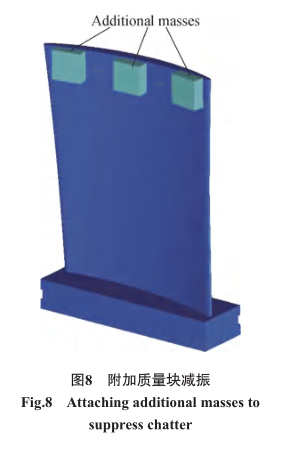
調(diào)諧質(zhì)量吸振器是一種常被用來附加于工件之上以增加工件被動阻尼進而實現(xiàn)加工振動抑制的裝置。
調(diào)諧質(zhì)量吸振器的工作原理為能量消耗,由質(zhì)量塊、彈簧和阻尼原件組成[90] 。此外,通過切削過程中采集的振動和切削力等信號進行顫振實時判斷,并利用磁流變液[91] 、壓電陶瓷[92]等智能材料開發(fā)驅(qū)動器,對振動系統(tǒng)施加外部載荷制動從而主動抑制顫振的方法同樣能夠有效提高切削穩(wěn)定性,Butt 等[93]通過在機床主軸上安裝非接觸渦流阻尼,實現(xiàn)了薄壁葉片類零件銑削抑振,并驗證了其阻尼可控性與復雜切削路徑的適應性。主動方法雖然可獲得較好的顫振抑制效果,但主動控制系統(tǒng)較為復雜,穩(wěn)定性不足。
合理的輔助支撐可以加固工件薄弱環(huán)節(jié),提高薄壁件切削系統(tǒng)剛度,有利于抑制切削振動和減小加工變形,從而提高加工質(zhì)量和加工效率。目前,輔助支撐加工方法主要包括填充物輔助支撐以及工裝輔助支撐等。填充物輔助支撐通過在容器中或薄壁框內(nèi)添加填充材料,如相變材料、低熔點合金、石蠟等,以達到增強薄弱環(huán)節(jié)加工剛度的目的。葛茂杰
[94]利用石蠟填充進行鈦合金薄壁件腹板和側壁的銑削,提高了加工穩(wěn)定性,減小了加工變形。Liu 等[95]通過比較有無氣射流輔助支撐的 Ti-6Al-4V 薄壁零件銑削動力學特性,證明了氣射流輔助支撐可以提高切削穩(wěn)定性并降低切削力,從而改善表面質(zhì)量并減小零件變形。
(2)優(yōu)化刀具參數(shù)和切削參數(shù)。
賈興民[96]針對鈦合金腹板切削易振動問題,基于銑削系統(tǒng)動力學模型分析了抑制腹板振動的策略,在保證加工效率的前提下,從刀具結構角度進行了抑制鈦合金腹板振動的刀具底刃開發(fā)設計。通過優(yōu)化切削參數(shù)同樣可以起到提高鈦合金結構件切削過程穩(wěn)定性的作用。李紅衛(wèi)等[97]通過對薄壁鈦合金零件加工動力學分析,建立了以顫振幅值為約束條件,材料去除效率為目標的切削參數(shù)優(yōu)化函數(shù)。Tunc 等[98]研究了刀具后角、后刀面幾何結構等刀具參數(shù)以及徑向切削深度等切削參數(shù)對切削過程阻尼影響規(guī)律,指出具有圓弧過渡的后刀面相比較平面型后刀面可以增加切削過程阻尼特性,提高切削穩(wěn)定性。此外,加速切削法與調(diào)速切削法也被認為可以有效抑制切削顫振[99-100] 。
復合能場鈦合金加工新技術
除了傳統(tǒng)的鈦合金切削加工研究,國內(nèi)外學者圍繞超聲、激光等多能場鈦合金復合加工進行了相關研究。
1、超聲振動輔助加工
超聲振動輔助加工(UltrasonicVibration assisted machining, UVAM)技術指的是在切削過程中,給刀具或者工件施加特定方向上的超聲頻段的微米級振動,從而達到降低切削力、提高加工表面質(zhì)量、延長刀具壽命的目的[101] 。
將超聲振動應用于鈦合金的銑削加工過程研究較少,近幾年才引起學者的關注。Ni 等[102]提出了一種用于分析超聲振動輔助銑削過程中刀具與工件接觸率的解析模型,通過試驗研究加工參數(shù)對 Ti-6Al-4V 超聲振動輔助加工性能的影響、結果表明,UVAM 方法在降低切削力、提高工件表面質(zhì)量、抑制毛刺形成等方面具有明顯的優(yōu)勢。
與常規(guī)銑削相比,Tong 等[103]的研究表明薄壁鈦合金銑削過程中的超聲振動輔助加工可以降低切削力,提高表面質(zhì)量以及減少振紋的產(chǎn)生。Liu [104] 、Han [105] 等通過對超聲橢圓振動輔助 Ti-6Al-4V 高速銑削研究,證明橢圓振動 UVAM 具有延長刀具壽命、產(chǎn)生更短更薄的切屑、并在合適的參數(shù)水平下降低切削力的作用。此外,這種方法還產(chǎn)生了更高的殘余壓應力,但是對于表面粗糙度來說,僅有合適的超聲參數(shù)與切削參數(shù)匹配才能獲得更低的表面粗糙度數(shù)值,大部分情況下,超聲橢圓振動輔助加工鈦合金會對表面質(zhì)量產(chǎn)生不利影響,如圖 9 所示[105] 。
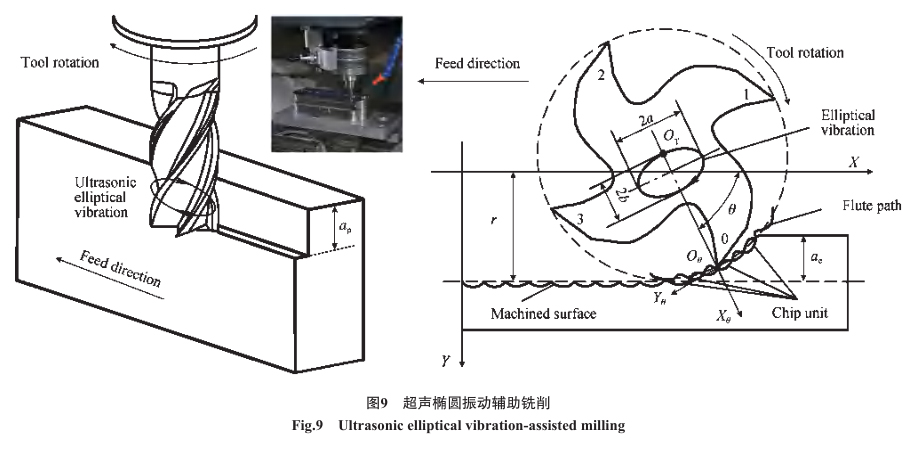
2、激光輔助加工
激光輔助加工(Laser-assistedmachining,LAM)通過引入高能量密度的激光源,對切削區(qū)域待加工部位的材料進行局部加熱,改變材料切削性能,從而達到降低切削力、提高
切削效率的目的[106] 。激光輔助加工技術在 20 世紀 70 年代提出,大多用于高硬度、高脆性材料,如工程陶瓷、工具鋼等。鈦合金激光輔助切削加工技術目前研究較少,主要集中在切削力方面。Dandekar等[107]研究了 TiAlN涂層硬質(zhì)合金刀具 LAM 鈦合金 Ti-6Al-4V 的加工性能,切削速度可達200m/min,相比于傳統(tǒng)加工手段,刀具壽命提升 2~3 倍。Bermingham 等[108]認為,硬質(zhì)合金刀具進行鈦合金高速車削時,刀具的黏結磨損與擴散磨損機制占主導地位,輔助加熱切削雖然可以降低切削力,但溫度升高的同時對刀具壽命會產(chǎn)生不利影響;但在銑削等斷續(xù)加工過程中,刀具破損占主導地位,加熱輔助切削會對刀具壽命帶來有益的影響。高延峰等[109]通過試驗證明了激光輔助銑削鈦合金有助于減小材料剪切抗力,同時指出切屑向連續(xù)型演變,絕熱剪切帶變得不再明顯。
目前,對于鈦合金 LAM 中切削機理的研究較少,LAM 是一項復雜的多能場復合加工技術,高溫下的材料摩擦行為與分離規(guī)律需要進一步的研究,高溫下刀具磨損機理也需要深入揭示。
結論
鈦合金結構件加工過程面臨材料與結構難加工性的雙重挑戰(zhàn),目前 PCD、PCBN 刀具雖然可以用于鈦合金高速切削,但存在成本高、耐沖擊性不足的缺點,硬質(zhì)合金刀具仍然是鈦合金結構件加工的主力刀具。但是硬質(zhì)合金刀具加工鈦合金刀具損耗嚴重,效率不足,需要大量使用切削液,與綠色加工趨勢相違背,工業(yè)界對鈦合金加工新型刀具材料、涂層材料以及刀具結構的需求永無止境,我國在該領域與國外技術水平還存在一定的差距,特別是高端刀具領域,需進一步加強研發(fā)力度。工藝優(yōu)化方面,綜合考慮加工質(zhì)量、刀具壽命、生產(chǎn)成本等多目標優(yōu)化方案尚需系統(tǒng)研究,不同冷卻潤滑介質(zhì)在刀具、工件、切屑中的耦合作用機理仍然需要深入揭示,從而避免工藝方案制定與切削液選用的盲目性,為實際生產(chǎn)提供切實指導。總體來說,鈦合金加工是一項系統(tǒng)工程,還涉及機床、夾具等,目前鈦合金難加工屬性并未改變,亟待通過變革性的工藝進步,突破鈦合金結構件加工質(zhì)量與加工效率提升的瓶頸難題,推動航空制造技術進步。
參考文獻
[1] 吳小燕. 一文了解2020年中國鈦合金材料發(fā)展現(xiàn)狀及競爭格局[EB/OL]. [2020-09-28]. https://www.qianzhan.com/analyst/detail/220/200927-00b70a52.html.WU Xiaoyan. A text to understand thedevelopment status and competition pattern oftitanium alloy materials in China in 2020[EB/OL]. [2020-09-28]. https://www.qianzhan.com/analyst/detail/220/200927-00b70a52.html.
[2] 劉志成, 張利軍, 薛祥義. 關于先進戰(zhàn)斗機結構制造用鈦概述[J]. 航空制造技術,2017, 60(6): 76-83.LIU Zhicheng, ZHANG Lijun, XUEXiangyi. Overview about advanced fighteraircraft structure made with titanium[J].Aeronautical Manufacturing Technology, 2017,60(6): 76-83.
[3] 孫玉晶. 鈦合金銑削加工過程參量建模及刀具磨損狀態(tài)預測[D]. 濟南: 山東大學, 2014.SUN Yujing. Arametric modeling ofmilling titanium alloy and prediction of tool
wear state[D]. Jinan: Shandong University,2014.
[4] 湘子. 硬質(zhì)合金晶粒度分級標準[J].
硬質(zhì)合金, 2006(2): 68-68.
XIANG Zi. Cemented carbide grain size
classification standards[J]. Cemented Carbide,
2006(2): 68-68.
[5] 張輝, 鄧建新, 李桂玉. 晶粒尺寸對
WC硬質(zhì)合金刀具材料摩擦磨損性能的影響
[J]. 工具技術, 2010(6): 9-12.
ZHANG Hui, DENG Jianxin,LI Guiyu.
Effects of WC grain size on friction and
wear behavior of WC cemented carbide tool
material[J]. Tool Engineering, 2010(6): 9-12.
[6] 陸劍中, 孫家寧. 金屬切削原理與刀
具[M]. 北京: 機械工業(yè)出版社, 2011.
LU Jianzhong, SUN Jianing. Metal cutting
principle and cutting tool[M]. Beijing: China
Machine Press, 2011.
[7] 程劍兵. 鎢鈷類超細硬質(zhì)合金刀具
及其切削性能研究[D]. 北京: 北京理工大學,
2015.
CHENG Jianbing. Research on cutting
performance of WC-Co ultrafine cemented
carbide cutting tools[D]. Beijing: Beijing
Institute of Technology, 2015.
[8] 曾瑞霖, 龍寧華, 肖躍勇, 等. 硬質(zhì)合
金刀具材料主要物理力學性能對鈦合金銑削
加工的影響[J]. 硬質(zhì)合金, 2019, 36(1): 82-86.
ZENG Ruilin, LONG Ninghua, XIAO
Yueyong, et al. Effect of physical and
mechanical properties of cutting tool materials
on titanium milling[J]. Cemented Carbide, 2019,
36(1): 82-86.
[9] 李友生. 硬質(zhì)合金刀具與Ti-6Al-4V
鈦合金的化學性能匹配研究[D]. 濟南: 山東大
學, 2010.
LI Yousheng. Chemical performance match
between cemented carbide tools and Ti-6Al-4V
alloy[D]. Jinan: Shandong University, 2010.
[10] 石磊. 鈦合金切削加工中刀具與工
件性能匹配的研究[D]. 濟南: 山東大學, 2007.
SHI Lei. Research on matching of
cutting tools and workpieces of titanium alloy
machining[D]. Jinan: Shandong University,
2007.
[11] 王文廣, 張賀佳, 王全兆, 等. 碳化
物抑制劑對WC-2.5TiC-10Co超細晶硬質(zhì)合
金微觀組織及力學性能的影響[J]. 材料研究
學報, 2015, 29(12): 881-888.
WANG Wenguang, ZHANG Hejia, WANG
Quanzhao, et al. Effects of carbide inhibitor on
microstructures and mechanical properties of
ultrafine grained carbide cement WC-2.5TiC-
10Co[J]. Chinese Journal of Materials Research,
2015, 29(12): 881-888.
[12] ZHOU X, WANG K, LI C, et al.
Effect of ultrafine gradient cemented carbides
substrate on the performance of coating tools
for titanium alloy high speed cutting[J].
International Journal of Refractory Metals and
Hard Materials, 2019, 84: 105024.
[13] SAINI A, PABLA B S, DHAMI S
S. Developments in cutting tool technology in
improving machinability of Ti-6Al-4V alloy:
A review[J]. Proceedings of the Institution
of Mechanical Engineers, Part B: Journal of
Engineering Manufacture, 2016, 230(11): 1977-
1989.
[14] 杜敏, 姜增輝, 馮吉路. 鈦合金切削
加工特點及刀具材料選用[J]. 航空制造技術,
2011, 54(14): 55-57.
DU Min, JIANG Zenghui, FENG Jilu.
Characteristics of machining titanium alloys
and the choice of tool material[J]. Aeronautical
Manufacturing Technology, 2011, 54(14): 55-57.
[15] POLINI W, TURCHETTA S. Cutting
force, tool life and surface integrity in milling
of titanium alloy Ti-6Al-4V with coated
carbide tools[J]. Proceedings of the Institution
of Mechanical Engineers, Part B: Journal of
Engineering Manufacture, 2016, 230(4): 694-700.
[16] 隋旭東, 李國建, 王強, 等. 鈦合金
切削用Ti 1-x Al x N涂層的制備及其切削性能研
究[J]. 金屬學報, 2016, 52(6): 741-746.
SUI Xudong, LI Guojian, WANG Qiang,
et al. Preparation of Ti 1-x Al x N coating in cutting
titanium alloy and its cutting performance[J].
Acta Metallurgica Sinica, 2016, 52(6): 741-746.
[17] JOY N, PRAKASH S, KRISHNA-
MOORTHY A, et al. Experimental investigation
and analysis of drilling in grade 5 titanium alloy
(Ti-6Al-4V)[J]. Materials Today: Proceedings,
2020, 21: 335-339.
[18] PéREZ J, LLORENTE J I, SANCHEZ
J A. Advanced cutting conditions for the milling
of aeronautical alloys[J]. Journal of Materials
Processing Technology, 2000, 100(1-3): 1-11.
[19] JAFFERY S H I, MATIVENGA P
T. Wear mechanisms analysis for turning Ti-
6Al-4V towards the development of suitable
tool coatings[J]. The International Journal of
Advanced Manufacturing Technology, 2012,
58(5-8): 479-493.
[20] 張勤儉, 趙路明, 劉敏之, 等. 刀具
涂層技術的研究現(xiàn)狀和發(fā)展趨勢[J]. 有色金
屬科學與工程, 2014, 5(2): 20-25.
ZHANG Qinjian, ZHAO Luming, LIU
Minzhi, et al. Research status and development
trends of cutting tool coating technology[J].
Nonferrous Metals Science and Engineering,
2014, 5(2): 20-25.
[21] 王云, 謝小豪, 汪艷亮, 等. 硬質(zhì)合
金刀具涂層的研究進展[J]. 有色金屬科學與
工程, 2019, 10(1): 60-66.
WANG Yun, XIE Xiaohao, WANG
Yanliang, et al. Latest progress in the
preparation of cemented carbide tool coatings[J].
Nonferrous Metals Science and Engineering,
2019,10(1): 60-66.
[22] NIU Q L, CHEN M, MING W W,
et al. Evaluation of the performance of coated
carbide tools in face milling TC6 alloy under
dry condition[J]. The International Journal of
Advanced Manufacturing Technology, 2013,
64(5-8): 623-631.
[23] 潘晨曦, 陳康華, 徐銀超,等. 添加
Cu對PVD AlTiN涂層組織結構和性能的影響
[J]. 粉末冶金材料科學與工程, 2016, 21(5):
717-721.
PAN Chenxi, CHEN Kanghua, XU
Yinchao, et al. Effect of adding Cu on structure
and cutting performance of PVD AlTiN
coating[J]. Materials Science and Engineering
of Powder Metallurgy, 2016, 21(5): 717-721.
[24] CHANG Y Y, LAI H M. Wear
behavior and cutting performance of CrAlSiN
and TiAlSiN hard coatings on cemented carbide
cutting tools for Ti alloys[J]. Surface and
Coatings Technology, 2014, 259: 152-158.
[25] 肖白軍. AlCrN/AlTiSiN納米多層
刀具涂層的制備及其性能研究[D]. 廣州: 廣東
工業(yè)大學, 2019.
XIAO Baijun. Fabrication and properties
of AlCrN/AlTiSiN nano-layered coatings
on cutting tools[D]. Guangzhou: Guangdong
University of Technology, 2019.
[26] LIAN Y, LONG Y, ZHAO G, et al.
Performance of CrCN-WS2 hard/soft composite
coated tools in dry cutting of titanium alloys[J].
Journal of Manufacturing Processes, 2020, 54:
201-209.
[27] OGANYAN M, VERESCHAKA
A, VOLOSOVA M, et al. Influence of the
application of wear-resistant coatings on force
parameters of the cutting process and the tool
life during end milling of titanium alloys[J].
Materials Today: Proceedings, 2021, 38: 1428-
1432.
[28] Lü W, LI G, ZHOU Y, et al. Effect
of high hardness and adhesion of gradient
TiAlSiN coating on cutting performance
of titanium alloy[J]. Journal of Alloys and
Compounds, 2020, 820: 153137.
[29] GUPTA K, LAUBSCHER R F.
Sustainable machining of titanium alloys: A
critical review[J]. Proceedings of the Institution
of Mechanical Engineers, Part B: Journal of
Engineering Manufacture, 2017, 231(14): 2543-
2560.
[30] 陳乾. PCD刀具前刀面光整加工試
驗研究[D]. 大連: 大連理工大學, 2020.
CHEN Qian. Experimental research on
finishing rake face of PCD tools[D]. Dalian:
Dalian University of Technology, 2020.
[31] FUNIK R D C. Characteristics and
cutting application of polycrystalline cubic
boron nitride cutting tools [EB/OL].[2020-06-
20].https://en.funik.com/faq/Characteristics-
and-cutting-application-of-polycrystalline-
cubic-boron-nitride-cutting-cutting-tools.html.
[32] AMIN A K M N, ISMAIL A F,
KHAIRUSSHIMA M K N. Effectiveness of
uncoated WC-Co and PCD inserts in end milling
of titanium alloy—Ti-6Al-4V[J]. Journal of
Materials Processing Technology, 2007, 192:
147-158.
[33] LINDVALL R, LENRICK F, PERSSON
H, et al. Performance and wear mechanisms of
PCD and PCBN cutting tools during machining
titanium alloy Ti6Al4V[J]. Wear, 2020, 454:
203329.
[34] REN Z J, QU S G, ZHANG Y L, et
al. Machining performance of PCD and PCBN
tools in dry turning titanium alloy Ti-6Al-
0.6Cr-0.4Fe-0.4Si-0.01B[J]. The International
Journal of Advanced Manufacturing Technology,
2019, 102(5-8): 2649-2661.
[35] 皇攀凌. 面向鈦合金銑削的變齒距
立銑刀研究[D]. 濟南: 山東大學, 2011.
HUANG Panling. Research on variable
pitch end mill in milling titanium alloy[D].
Jinan: Shandong University, 2011.
[36] SHAHARUN M A, YUSOFF A
R. Effects of irregular tool geometry and
machining process parameters on the
wavelength performance of process damping
in machining titanium alloy at low cutting
speed[J]. The International Journal of Advanced
Manufacturing Technology, 2016, 85(5-8):
1019-1033.
[37] IGLESIAS A, DOMBOVARI Z,
GONZALEZ G, et al. Optimum selection of
variable pitch for chatter suppression in face
milling operations[J]. Materials, 2019, 12(1): 112.
[38] DANIYAN I, TLHABADIRA I,
MPOFU K, et al. Investigating the geometrical
effects of cutting tool on the surface roughness
of titanium alloy (Ti-6Al-4V) during milling
operation[J]. Procedia CIRP, 2021, 99: 157-164.
[39] MONIES F, FREDJ M, SENATORE
J, et al. Influence of a cutter’s main geometrical
parameters on cutting forces in plunge milling
of Ti-6Al-4V[J]. The International Journal of
Advanced Manufacturing Technology, 2020,
108(11-12): 3835-3858.
[40] 劉月萍. 銑削Ti-6A1-4V刀具刃口
鈍化研究[D]. 濟南: 山東大學, 2010.
LIU Yueping. Study on the tool edge
preparation for milling Ti-6A1-4V[D]. Jinan:
Shandong University, 2010.
[41] ARAUJO A C, FROMENTIN G,
BLANDENET P. Investigation on PCD
cutting edge geometry for Ti-6A1-4V high-
feed milling[J]. The International Journal of
Advanced Manufacturing Technology, 2020,
111(5-6): 1785-1796.
[42] 姜振喜. TC4-DT鈦合金切削性能
研究與仿生刀具結構設計[D]. 濟南: 山東大
學, 2016.
JIANG Zhenxi. Research on machinability
of TC4-DT titanium alloy and structural design
of bionic tool[D]. Jinan: Shandong University,
2016.
[43] 田汝坤. 銑削鈦合金薄壁件刀具結
構設計研究[D]. 濟南: 山東大學, 2012.
TIAN Rukun. Tool structures design for
milling titanium thin-walled parts[D]. Jinan:
Shandong University, 2012.
[44] ZHU Z, GUO K, SUN J, et al.
Evaluation of novel tool geometries in dry
drilling aluminium 2024-T351/titanium
Ti-6Al-4V stack[J]. Journal of Materials
Processing Technology, 2018, 259: 270-281.
[45] 田付新. 山高推出新型Turbo玉米
銑刀[J]. 金屬加工(冷加工), 2013(18): 6.
TIAN Fuxin. Seco introduces new Turbo
corn milling cutter[J]. Metal processing(Cold
working): 2013(18): 6.
[46] 章宗城. 航空工業(yè)難加工材料切削
刀具的新發(fā)展[J]. 現(xiàn)代制造, 2013(5): 62-64.
ZHANG Zongcheng. New developments in
cutting tools for difficult-to-machine materials in
the aviation industry[J]. Modern Manufacturing,
2013(5): 62-64.
[47] 李亮. 鈦合金的高速粗加工——
大進給銑削技術[J]. 航空制造技術, 2014,
57(12): 32-35.
LI Liang. High speed rough machining-
high feed milling of titanium alloys[J].
Aeronautical Manufacturing Technology, 2014,
57(12): 32-35.
[48] AKINCIO?LU S, G?KKAYA H,
UYGUR ?. A review of cryogenic treatment on
cutting tools[J]. The International Journal of
Advanced Manufacturing Technology, 2015,
78(9-12): 1609-1627.
[49] STRANO M, ALBERTELLI P,
CHIAPPINI E, et al. Wear behaviour of PVD
coated and cryogenically treated tools for Ti-
6Al-4V turning[J]. International Journal of
Material Forming, 2015, 8(4): 601-611.
[50] SIVALINGAM V, SUN J, SELVAM
B, et al. Experimental investigation of tool
wear in cryogenically treated insert during
end milling of hard Ti alloy[J]. Journal of the
Brazilian Society of Mechanical Sciences and
Engineering, 2019, 41(2): 1-14.
[51] REVURU R S, ZHANG J Z,
POSINASETTI N R, et al. Optimization of
titanium alloys turning operation in varied
cutting fluid conditions with multiple machining
performance characteristics[J]. The International
Journal of Advanced Manufacturing Technology,
2018, 95(1-4): 1451-1463.
[52] AKKU? H, YAKA H. Experimental
and statistical investigation of the effect of
cutting parameters on surface roughness,
vibration and energy consumption in machining
of titanium 6Al-4V ELI (grade 5) alloy[J].
Measurement, 2021, 167: 108465.
[53] HASHMI K H, ZAKRIA G, RAZA
M B, et al. Optimization of process parameters
for high speed machining of Ti-6Al-4V using
response surface methodology[J]. The International
Journal of Advanced Manufacturing Technology,
2016, 85(5-8): 1847-1856.
[54] JIANG F, LI J F, YAN L, et al.
Optimizing end-milling parameters for surface
roughness under different cooling/lubrication
conditions[J]. The International Journal of
Advanced Manufacturing Technology, 2010,
51(9-12): 841-851.
[55] GUPTA M K, SOOD P K, SHARMA
V S. Machining parameters optimization of
titanium alloy using response surface methodology
and particle swarm optimization under minimum-
quantity lubrication environment[J]. Materials and
Manufacturing Processes, 2016, 31(13): 1671-
1682.
[56] 孫玉晶, 孫杰, 李劍峰. 鈦合金銑削
加工刀具磨損有限元預測分析[J]. 機械工程
學報, 2016, 52(5): 193-201.
SUN Yujing, SUN Jie, LI Jianfeng. Finite
element analysis on prediction of tool wear
in milling titanium[J]. Journal of Mechanical
Engineering, 2016, 52(5): 193-201.
[57] ISAKSON S, SADIK M I,
MALAKIZADI A, et al. Effect of cryogenic
cooling and tool wear on surface integrity of turned
Ti-6Al-4V[J]. Procedia CIRP, 2018, 71: 254-259.
[58] SUN S, BRANDT M, DARGUSCH
M S. Machining Ti-6Al-4V alloy with cryogenic
compressed air cooling[J]. International Journal
of Machine Tools & Manufacture, 2010, 50(11):
933-942.
[59] GARCíA-MARTíNEZ E, MIGUEL V,
MARTíNEZ-MARTíNEZ A, et al. Sustainable
lubrication methods for the machining of
titanium alloys: An overview[J]. Materials,<2019, 12(23): 1-22.
[60] MIA M, DHAR N R. Effects of
duplex jets high-pressure coolant on machining
temperature and machinability of Ti-6Al-4V
superalloy[J]. Journal of Materials Processing
Technology, 2018, 252: 688-696.
[61] JEROLD B D, KUMAR M P. The
influence of cryogenic coolants in machining
of Ti-6Al-4V[J]. Journal of Manufacturing
Science & Engineering, 2013, 135(3): 922-926.
[62] AGRAWAL C, WADHWA J,
PITRODA A, et al. Comprehensive analysis of
tool wear, tool life, surface roughness, costing and
carbon emissions in turning Ti–6Al–4V titanium
alloy: Cryogenic versus wet machining[J].
Tribology International, 2021, 153: 106597.
[63] SADIK M I, ISAKSON S,
MALAKIZADI A, et al. Influence of coolant
flow rate on tool life and wear development in
cryogenic and wet milling of Ti-6Al-4V[J].
Procedia CIRP, 2016, 46: 91-94.
[64] SHOKRANI A, DHOKIA V,
NEWMAN S T. Investigation of the effects
of cryogenic machining on surface integrity
in CNC end milling of Ti-6Al-4V titanium
alloy[J]. Journal of Manufacturing Processes,
2016, 21: 172-179.
[65] JAMIL M, HE N, ZHAO W, et al.
Heat transfer efficiency of cryogenic-LN2 and
CO 2 -snow and their application in the turning
of Ti-6AL-4V[J]. International Journal of Heat
and Mass Transfer, 2021, 166: 120716.
[66] TANVEER A, MARLA D,
KAPOOR S G. A thermal model to predict tool
temperature in machining of Ti-6Al-4V alloy
with an atomization-based cutting fluid spray
system[J]. Journal of Manufacturing Science
and Engineering, 2017, 139(7): 071016.
[67] SINGH R, DUREJA J S, DOGRA
M, et al. Wear behavior of textured tools under
graphene-assisted minimum quantity lubrication
system in machining Ti-6Al-4V alloy[J].
Tribology International, 2020, 145: 106183.
[68] SHOKRANI A, AL-SAMARRAI
I, NEWMAN S T. Hybrid cryogenic MQL for
improving tool life in machining of Ti-6Al-
4V titanium alloy[J]. Journal of Manufacturing
Processes, 2019, 43: 229-243.
[69] PERVAIZ S, ANWAR S, QURESHI
I, et al. Recent advances in the machining
of titanium alloys using minimum quantity
lubrication (MQL) based techniques[J].
International Journal of Precision Engineering
and Manufacturing-Green Technology, 2019,
6(1): 133-145.
[70] PAWADE R S, REDDY D S N,
KADAM G S. Chip segmentation behaviour
and surface topography in high-speed turning
of titanium alloy (Ti-6Al-4V) with eco-
friendly water vapour[J]. International Journal
of Machining and Machinability of Materials,
2013, 13(2-3): 113-137.
[71] GANGULI S, KAPOOR S G.
Improving the performance of milling of
titanium alloys using the atomization-based
cutting fluid application system[J]. Journal of
Manufacturing Processes, 2016, 23: 29-36.
[72] OSMAN K A, üNVER H ?, ?EKER
U. Application of minimum quantity lubrication
techniques in machining process of titanium
alloy for sustainability: A review[J]. The
International Journal of Advanced Manufacturing
Technology, 2019, 100(9-12): 2311-2332.
[73] LIU J, HAN R, LI Z, et al. Study
on lubricating characteristic and tool wear with
water vapor as coolant and lubricant in green
cutting[J]. Wear, 2007, 262(3-4): 442-452.
[74] JAMIL M, HE N, ZHAO W, et al.
Tribological behavior of WC-6Co against Ti-
6Al-4V alloy under novel cryogenic ethanolester
oil dry-ice hybrid lubri-cooling[J]. Tribology
International, 2021, 156: 106812.
[75] BAI X F, LI C H, DONG L, et al.
Experimental evaluation of the lubrication
performances of different nanofluids for
minimum quantity lubrication (MQL) in milling
Ti-6Al-4V[J]. The International Journal of
Advanced Manufacturing Technology, 2019,
101(9-12): 2621-2632.
[76] LI M, YU T B, ZHANG R C, et
al. MQL milling of TC4 alloy by dispersing
graphene into vegetable oil-based cutting
fluid[J]. The International Journal of Advanced
Manufacturing Technology, 2018, 99(5-8):
1735-1753.
[77] LI G, YI S, LI N, et al. Quantitative
analysis of cooling and lubricating effects
of graphene oxide nanofluids in machining
titanium alloy Ti-6Al-4V[J]. Journal of
Materials Processing Technology, 2019, 271:
584-598.
[78] YI S, LI G, DING S, et al. Performance
and mechanisms of graphene oxide suspended
cutting fluid in the drilling of titanium alloy Ti-
6Al-4V[J]. Journal of Manufacturing Processes,
2017, 29: 182-193.
[79] REVURU R S, ZHANG J Z,
POSINASETTI N R, et al. Optimization of
titanium alloys turning operation in varied
cutting fluid conditions with multiple machining
performance characteristics[J]. The International
Journal of Advanced Manufacturing Technology,
2018, 95(1-4): 1451-1463.
[80] LIU G T, LI C H, ZHANG Y B,
et al. Process parameter optimization and
experimental evaluation for nanofluid MQL in
grinding Ti-6Al-4V based on grey relational
analysis[J]. Materials and Manufacturing
Processes, 2018, 33(9): 950-963.
[81] SETTI D, SINHA M K, GHOSH
S, et al. An investigation into the application
of Al 2 O 3 nanofluid-based minimum quantity
lubrication technique for grinding of Ti-
6Al-4V[J]. International Journal of Precision
Technology, 2014, 4(3-4): 268-279.
[82] SINGH G, SHARMA V S. Analyzing
machining parameters for commercially pure
titanium (Grade 2), cooled using minimum
quantity lubrication assisted by a Ranque-Hilsch
vortex tube[J]. The International Journal of
Advanced Manufacturing Technology, 2017,
88(9-12): 2921-2928.
[83] MA?é I, GAGNOL V, BOUZGARROU
B C, et al. Stability-based spindle speed control
during flexible workpiece high-speed milling[J].
International Journal of Machine Tools and
Manufacture, 2008, 48(2): 184-194.
[84] 梁睿君, 葉文華. 薄壁零件高速銑
削穩(wěn)定性預測與驗證[J]. 機械工程學報, 2009,
45(11): 146-151.
LIANG Ruijun, YE Wenhua. Stability
prediction for high-speed milling of thin walled
structures and experimental validation[J].
Journal of Mechanical Engineering, 2009,
45(11): 146-151.
[85] WANG X, SONG Q, LIU Z.
Dynamic model and stability prediction of
thin-walled component milling with multi-
modes coupling effect[J]. Journal of Materials
Processing Technology, 2021, 288: 116869.
[86] YANG Y, WU D, LIU Q. Chatter
stability prediction of milling considering
nonlinearities[J]. Proceedings of the Institution
of Mechanical Engineers, Part B: Journal of
Engineering Manufacture, 2021, 235(5): 862-876.
[87] KOLLURU K, AXINTE D, BECKER
A. A solution for minimising vibrations in
milling of thin walled casings by applying
dampers to workpiece surface[J]. CIRP Annals,
2013, 62(1): 415-418.
[88] WAN M, DANG X B, ZHANG W H,
et al. Optimization and improvement of stable
processing condition by attaching additional
masses for milling of thin-walled workpiece[J].
Mechanical Systems and Signal Processing,
2018, 103: 196-215.
[89] YANG Y, WANG Y, LIU Q. Design
of a milling cutter with large length-diameter
ratio based on embedded passive damper[J].
Journal of Vibration and Control, 2019, 25(3):
506-516.
[90] RASHID A, NICOLESCU C M.
Design and implementation of tuned viscoelastic
dampers for vibration control in milling[J].
International Journal of Machine Tools and
Manufacture, 2008, 48(9): 1036-1053.
[91] 毋健雄. 磁流變勵磁固化特性對薄
壁件切削抑振的影響分析[D]. 大連: 大連理工
大學, 2019.
WU Jianxiong. Analysis of the influence
of magnetorheological excitation solidification
characteristics on cutting vibration suppression
of thin-walled parts[D]. Dalian: Dalian
University of Technology, 2019.
[92] ZHANG X, WANG C, LIU J,
et al. Robust active control based milling
chatter suppression with perturbation model
via piezoelectric stack actuators[J]. Mechanical
Systems and Signal Processing, 2019, 120: 808-
835.
[93] BUTT M A, YANG Y, PEI X,
et al. Five-axis milling vibration attenuation
of freeform thin-walled part by eddy current
damping[J]. Precision Engineering, 2018, 51:
682-690.
[94] 葛茂杰, 孫杰, 高彪, 等. 石蠟輔助
加固鈦合金薄壁件加工質(zhì)量分析[J]. 航空制
造技術, 2013, 56(10): 79-83.
GE Maojie, SUN Jie, GAO Biao, et al.
Processing quality analysis of thin-walled
titanium alloy component with paraffin
reinforcement[J]. Aeronautical Manufacturing
Technology, 2013, 56(10): 79-83.
[95] LIU C, SUN J, LI Y L, et al.
Investigation on the milling performance of
titanium alloy thin-walled part with air jet
assistance[J]. The International Journal of
Advanced Manufacturing Technology, 2018,
95(5-8): 2865-2874.
[96] 賈興民. 基于振動特性鈦合金腹板
加工刀具設計與性能評價[D]. 濟南: 山東大
學, 2015.
JIA Xingmin. The design and evaluation
of the cutting tool for titanium alloy web based
on the characteristics of vibration[D]. Jinan:
Shandong University, 2015.
[97] 李紅衛(wèi), 師智斌, 唐慧霖, 等. 薄壁
鈦合金零件切削顫振控制技術研究[J]. 航天
制造技術, 2015(2): 9-12.
LI Hongwei, SHI Zhibin, TANG Huilin,
et al. Research of cutting vibration control
technology for thin-walled titanium alloy parts[J].
Aerospace Manufacturing Technology, 2015(2):
9-12.
[98] TUN? L T, BUDAK E. Effect of
cutting conditions and tool geometry on process
damping in machining[J]. International Journal
of Machine Tools and Manufacture, 2012, 57:
10-19.
[99] HAYASAKA T, NAM S, JUNG
H, et al. Proposal of ‘a(chǎn)ccelerative cutting’ for
suppression of regenerative chatter[J].CIRP Annals-
Manufacturing Technology, 2018, 67(1): 401-404.
[100] BEDIAGA I , MUNOA J,
HERNANDEZ J , et al. An automatic spindle
speed selection strategy to obtain stability in
high-speed milling[J]. International Journal of
Machine Tools and Manufacture, 2009, 49(5):
384-394.
[101] 倪陳兵, 朱立達, 寧晉生, 等. 超聲
振動輔助銑削鈦合金銑削力信號及切屑特征
研究[J]. 機械工程學報, 2019, 55(7): 207-216.
NI Chenbing, ZHU Lida, NING Jinsheng,
et al. Research on the characteristics of cutting
force signal and chip in ultrasonic vibration-
assisted milling of titanium alloys[J]. Journal of
Mechanical Engineering, 2019, 55(7): 207-216.
[102] NI C, ZHU L, LIU C, et al. Analytical
modeling of tool-workpiece contact rate and
experimental study in ultrasonic vibration-
assisted milling of Ti-6Al-4V[J]. International
Journal of Mechanical Sciences, 2018, 142-143:
97-111.
[103] TONG J L, WEI G, ZHAO L, et al.
Surface microstructure of titanium alloy thin-
walled parts at ultrasonic vibration-assisted
milling[J]. The International Journal of
Advanced Manufacturing Technology, 2019,
101(1-4): 1007-1021.
[104] LIU J J, JIANG X G, HAN X, et al.
Influence of parameter matching on performance
of high-speed rotary ultrasonic elliptical
vibration-assisted machining for side milling
of titanium alloys[J]. The International Journal
of Advanced Manufacturing Technology, 2019,
101(5-8): 1333-1348.
[105] HAN X, ZHANG D Y. Effects of
separating characteristics in ultrasonic elliptical
vibration-assisted milling on cutting force, chip,
and surface morphologies[J]. The International
Journal of Advanced Manufacturing Technology,
2020, 108(9-10): 3075-3084.
[106] 吳雪峰, 王揚. 激光加熱輔助切
削技術及研究進展[J]. 哈爾濱理工大學學報,
2012,17(4): 34-45.
WU Xuefeng, WANG Yang. The
technology and development of laser assisted
machining[J]. Journal of Harbin University of
Science and Technology, 2012, 17(4): 34-45.
[107] DANDEKAR C R, SHIN Y C,
BARNES J. Machinability improvement of
titanium alloy (Ti–6Al–4V) via LAM and hybrid
machining[J]. International Journal of Machine
Tools and Manufacture, 2010, 50(2): 174-182.
[108] BERMINGHAM M J, PALANISAMY
S, DARGUSCH M S. Understanding the tool
wear mechanism during thermally assisted
machining Ti-6Al-4V[J]. International Journal
of Machine Tools and Manufacture, 2012, 62:
76-87.
[109] 高延峰, 肖建華. Ti-6Al-4V合金
激光輔助銑削的刀具磨損特性[J]. 中國機械
工程, 2016, 27(21): 2877-2883.
GAO Yanfeng, XIAO Jianhua. Characteristics
of cutting tool wear during lam processes
for Ti-6Al-4V alloy[J]. China Mechanical
Engineering, 2016, 27(21): 2877-2883.
相關鏈接