鈦合金TC4是一種中等強度的α-β型兩相鈦合金,含有6%α穩定元素Al和4%β穩定元素V。TC4具有優異的耐腐蝕、耐高溫和高比強度,在航空航天中獲得最廣泛的應用。TC4的比重較小、強度高、高溫強度突出。
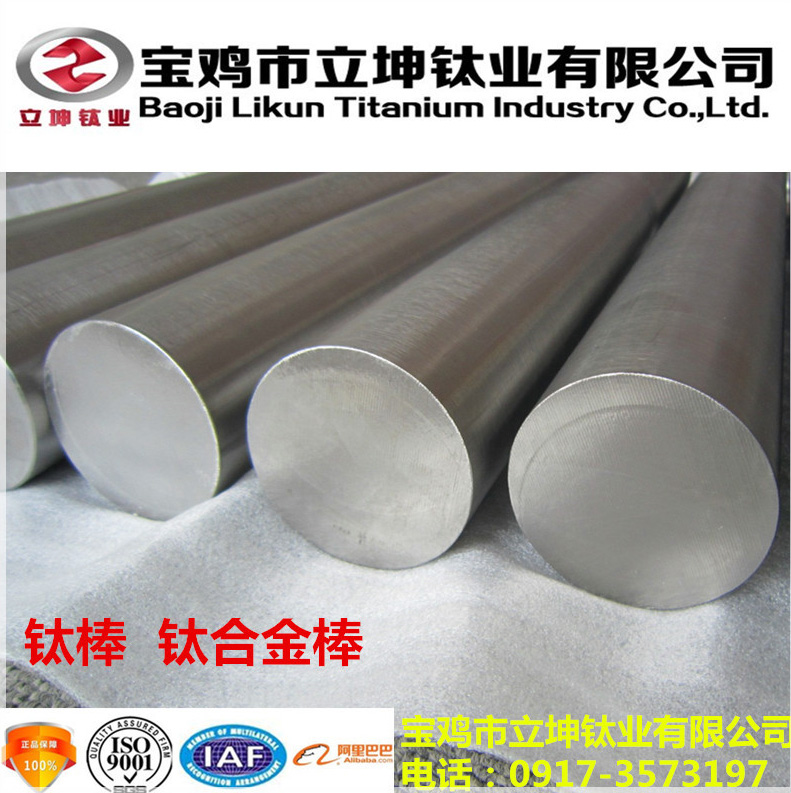
1Cr18Ni9Ti是奧氏體鉻鎳不銹鋼,具有優良的力學性能、良好的耐蝕能力、較突出的冷變形能力、無磁性等優點,在航空航天、機械制造及人們日常生活中得到了廣泛應用。由于鈦合金TC4與不銹鋼1Cr18Ni9Ti加工難度大、切削加工效率低、刀具磨損快、使兩種材料成為典型難加工材料。這兩種材料在物理、化學和機械性能上差異較大,對它們的加工性能進行研究,選擇合適的加工刀具材料,優化加工幾何參數,提高加工效率是迫切需要解決的問題。鈦合金TC4與不銹鋼1Cr18Ni9Ti切削加工性分析比較見表1。表1 鈦合金TC4與不銹鋼1Cr18Ni9Ti切削加工性分析比較 材料 強度和硬度 不同 塑性變形 不同 導熱系數 不同 彈性模量 不同 活性 不同 TC4 硬度和強度較高,硬度359HV,常溫下抗拉強度≥895MPa 延伸率小 (為10%) 導熱系數很小 (為7.955W/m·K) 彈性模量為110GPa 化學活性大 1Cr18Ni9Ti 硬度為187HV, 抗拉強度為520MPa 延伸率大 (為45%) 導熱系數大 (為16.2W/m·K) 彈性模量為206GPa 加工硬化性大,親和性大 根據以上對兩種材料切削加工性的比較分析,不難發現TC4主要為材料硬度高、強度大、導熱系數小、彈性模量大、化學活性大,特別是高溫強度高,導致切削力大;材料導熱性能差、摩擦現象嚴重,易造成刀尖和切削刃上切削熱非常集中,致使切削溫度很高;高溫下刀具材料和TC4材料雙方化學元素的相互擴散造成擴散磨損,高溫還使刀具材料與周圍介質發生化學反應造成化學磨損。而1Cr18Ni9Ti主要為材料延伸率大、加工硬化性大、親和性大,故在切削過程中的塑性變形較大、使車削力增加;工件材料塑性變形大,與刀具之間的摩擦也大,切削過程中產生的切削熱多,致使切削溫度較高;不銹鋼親和性大,粘附性強,因而刀具在切削過程中易形成積屑瘤,使表面的粗糙度降低;不銹鋼中由碳化物形成的硬質點使刀具磨損加劇。因此,合理選擇刀具材料成為解決這兩種材料加工效率低的關鍵。刀具材料的選擇應首先以降低切削溫度、減小刀具磨損為首要考慮的因素。要求刀具材料有高的硬度和強度,良好的耐磨性以及韌性,較高的耐熱性等。除此之外,選擇刀具材料時還應特別注意避免因刀具材料和工件材料之間某些元素的親和作用致使刀具磨損加劇。 TC4和1Cr18Ni9Ti都不能使用YT類硬質合金加工,要選用與Ti元素親和作用小、導熱性能好、強度高的細晶粒YG類硬質合金如YG6、YG8、YG6X、YG6A等刀具材料。按照國際上對加工材料的分類選擇刀具材料,TC4一般選擇S類刀具材料;1Cr18Ni9Ti一般選擇M類刀具材料。
相關鏈接