1、技術(shù)標(biāo)準(zhǔn)
1.1 鈦管的設(shè)計(jì)技術(shù)條件與標(biāo)準(zhǔn)
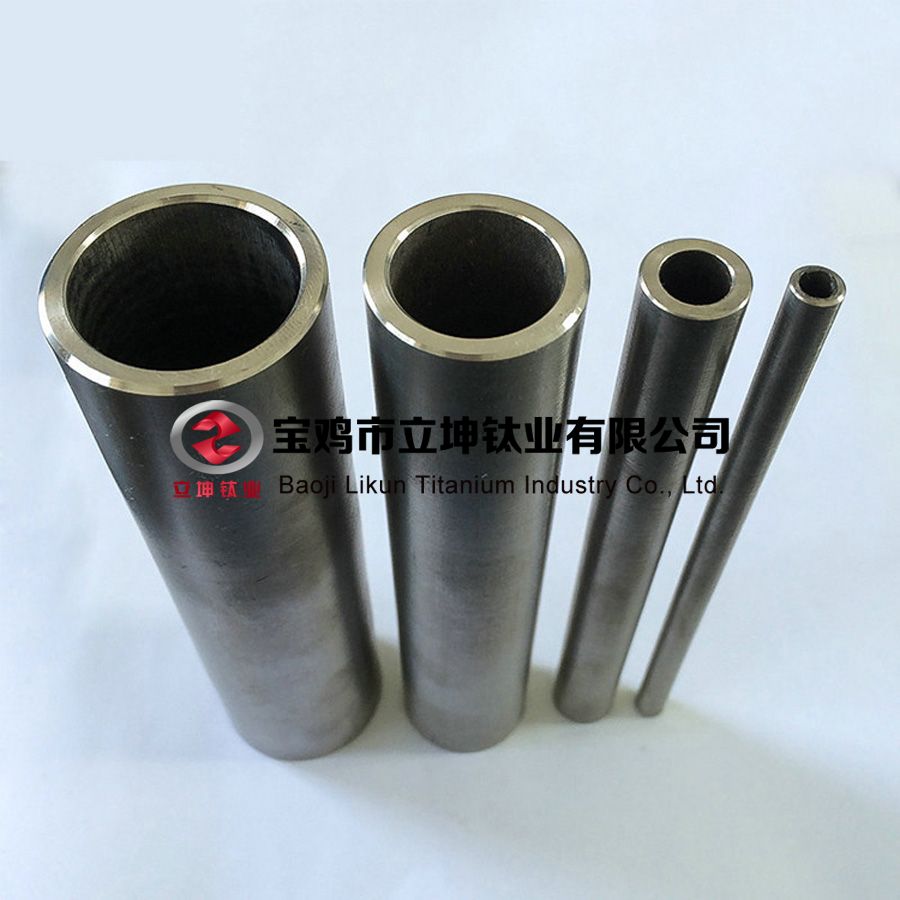
1.1.1 設(shè)計(jì)技術(shù)條件
1.1.1.1 管材及配件材質(zhì)IN17850 3.7025,3.7035,3.7055.其化學(xué)成分如下表:序號(hào)材料號(hào)牌號(hào)化學(xué)成分DINl7850 (級(jí)別) Ti C Fe N O H
1 3.7025 余量≤0.08 ≤0.20 ≤0.05 0.03~0.12 ≤0.013
2 3.7035 Ⅱ余量≤0.08 ≤0.25 ≤0.05 0.07~0.18 ≤0.013
3 3.7055 Ⅲ余量≤0.10 ≤0.30 ≤0.05 0.15~0.25 ≤0.013
1.1.1.2 管材規(guī)格:φ508×4.5,φ408×14,φ26.9×l.5,φ21.3×2.6。
1.1.1.3 鈦管工作條件;溫度224℃,壓力2.5MPa,介質(zhì)醋酸,溴化物。
1.1.1.4 管道質(zhì)量要求:焊接接頭系數(shù)1,焊縫射線檢驗(yàn)100%,水壓試驗(yàn)力3.75MPa,氣密性試驗(yàn)壓力0.625MPa
1.1.2 技術(shù)標(biāo)準(zhǔn)
1.1.2.1 管道工程鈦材焊接規(guī)范LON1015E
1.1.2.2 鈦管施工技術(shù)條件伍德公司標(biāo)準(zhǔn)
1.1.2.3 鈦管施工及驗(yàn)收規(guī)范SHJ502-86
1.2 焊接特點(diǎn)
鈦管焊接是利用惰性氣體對(duì)焊接區(qū)進(jìn)行有效保護(hù)的TiG焊接工藝。由于鈦材具有特殊的物理化學(xué)特性,因而其焊接工藝與其它金屬存在較大差異。焊接時(shí)必須保證:(1)焊接區(qū)金屬在250℃以上不受活性氣體N,0、H
及有害雜質(zhì)元素C,F(xiàn)e,Mn等的污染。(2)不能形成粗晶組織。(3)不能產(chǎn)生較大的焊接殘余應(yīng)力和殘余變形。所以,焊接過(guò)程須按合
理的工藝,嚴(yán)格按工序質(zhì)量管理標(biāo)準(zhǔn),實(shí)行全過(guò)程的質(zhì)量控制。使人、機(jī)、料、法各因素均
處于良好的受控狀態(tài),從而在合理的工期內(nèi),保證鈦管的焊接質(zhì)量。
2、材料、設(shè)備及工具要求
2.1 鈦管及配件;應(yīng)具有制造廠的出廠合格證和質(zhì)量證明書(shū)。經(jīng)復(fù)驗(yàn)其規(guī)格、化學(xué)成分、力學(xué)性能及供貨狀態(tài)均應(yīng)符合DIN17850標(biāo)準(zhǔn)的要求。
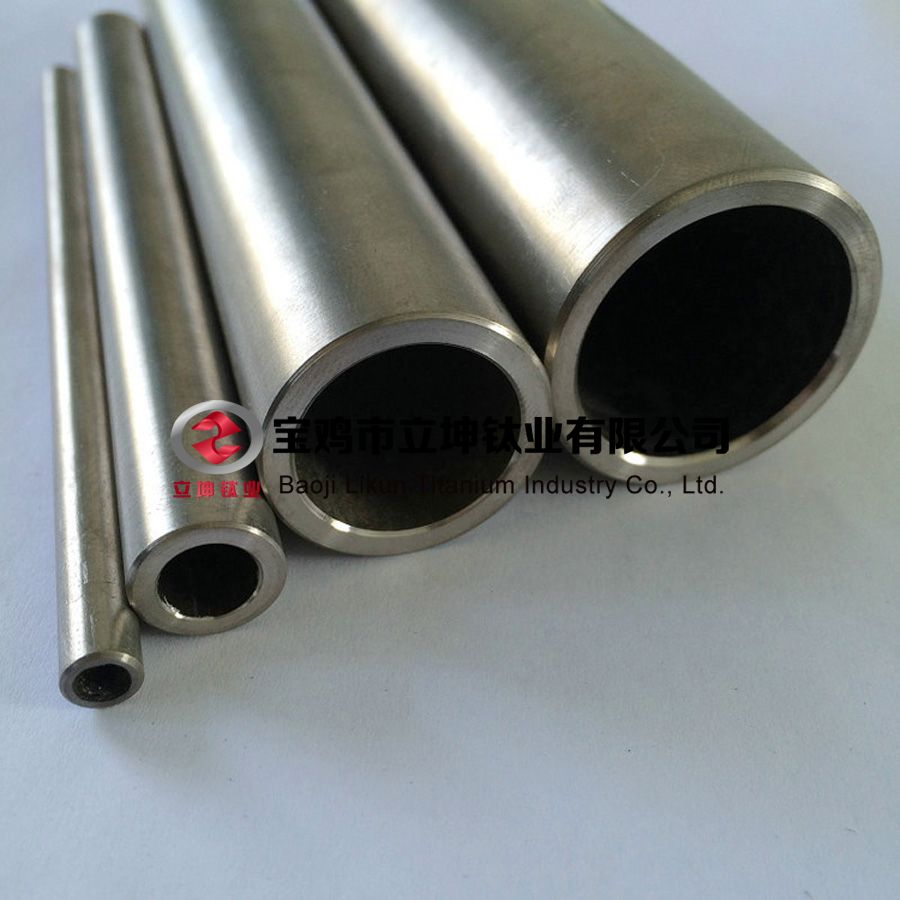
2.2 焊接材料
2.2.1 焊絲:焊絲牌號(hào)為ERTi-2。選擇焊絲應(yīng)符合:(1)焊絲的化學(xué)成分和力學(xué)性能應(yīng)與母材相當(dāng);(2)若焊件要求有較高的塑性時(shí),應(yīng)采用純度比母材高的焊絲。
2.2.2 焊絲在使用前要進(jìn)行材質(zhì)復(fù)驗(yàn),檢查出廠合格證和質(zhì)量證明書(shū);焊絲表面應(yīng)清潔,無(wú)氧化色、無(wú)裂紋、起皮、斑疤和夾渣等缺陷。焊絲的化學(xué)成分應(yīng)符合AWS A5.16一70的有關(guān)規(guī)定。
2.2.3 氬氣:工業(yè)一級(jí) 純 氬,純度不得低于99.98%,含水量小于50Mg/L氬氣在使用前先檢查瓶體上的出廠合格證,以驗(yàn)證氫氣的純度指標(biāo),然后檢查瓶閥有無(wú)漏氣或失靈現(xiàn)象。
2.2.4 鎢極:選用φ2.0~φ3.0 mm鈰鎢極,其化學(xué)成分應(yīng)符合如下要求:
成份%
牌號(hào)W CeO Fe2O3+Al2O3 SiO2 Mo CuO
Wce-20 余量2.0 ≤0.02 ≤0.06 ≤0.01 ≤0.01
2.3 焊接設(shè)備
2.3.1 焊機(jī):采用直流TiG焊機(jī)。焊機(jī)應(yīng)保證優(yōu)良的工作特性和調(diào)節(jié)特性,
同時(shí)配備有完好的電流表和電壓表。
2.3.2 焊炬:采用QS一75°/500型水冷式TiG焊焊炬。焊炬應(yīng)具有結(jié)構(gòu)簡(jiǎn)單,輕巧耐用,槍體嚴(yán)密,絕緣良好,氣流穩(wěn)定,夾鎢捧牢固,適合于各種位置焊接的特點(diǎn)。
2.3.3 氬氣輸送管;采用半硬質(zhì)塑料管,不宜用橡膠軟管和其它吸濕材料。使用時(shí)應(yīng)專用,不得與輸送其它氣體的管相互串用。氬氣管不宜過(guò)長(zhǎng),以免壓力降過(guò)大引起氣流不穩(wěn),一般不超過(guò)30m。
2.3.4 焊接夾具:用奧氏體不銹鋼或銅制管卡蘭、鎖緊螺栓等組對(duì)鈦管及配件。應(yīng)確保對(duì)鈦管及配件有一定的夾緊力,以保證軸線一致,間隙均勻合適。
2.3.5 輔助設(shè)備及工具:氬氣保護(hù)罩,磨光機(jī),專用銼刀,不銹鋼絲刷等。
3、焊接工藝
3.1 管道預(yù)制階段
3.1.1 管道切割與坡口加工;管材切割與坡口加工應(yīng)在專門的作業(yè)場(chǎng)所內(nèi)采用機(jī)械加工方法進(jìn)行。加工時(shí)要用非污染介質(zhì)潔凈水進(jìn)行冷卻,以防氧化。加工工具應(yīng)專用,并保持清潔,以防鐵質(zhì)污染。加工好的管口應(yīng)保證表面平整,無(wú) 裂 紋、重皮等缺陷。切口平面最大傾斜度偏差不超過(guò)管徑的1%。
3.1.2 表面清理:用奧氏體不銹鋼制的鋼絲刷清除鈦管所有焊接表面及坡口附近100mm內(nèi) 的 銹 皮、油漆 、臟 物、灰 塵 和 能 與 鈦 材 起 反 應(yīng) 的 雜 物 。用砂 輪 修 整 加 工 面 , 清 除 飛 邊 、 毛 刺 、 凸凹等缺陷。
3.1.3 組對(duì):將 鈦 管、配 件 對(duì) 準(zhǔn)、夾 好, 軸 線 不 得 偏 移 ,間 隙 均 勻 一 致 ,并 應(yīng) 防 止 鈦 管 在 裝配中被損傷和污染。避免強(qiáng)制組對(duì)。定位焊采用和正式焊接相同的焊接工藝。
3.1.4 脫脂處理:用賽璐珞海棉沾無(wú)硫乙醇或無(wú)硫丙酮對(duì)所有焊接表面坡口附近50mm內(nèi)全部做脫脂處理,處理后的表面應(yīng)無(wú)任何殘留物。
3.1.5 焊接:應(yīng)在有關(guān)標(biāo)準(zhǔn)規(guī)定的條件下進(jìn)行。
3.1.5.1 焊接工藝評(píng)定
在鈦管正式施焊前,用φ252×14 TA2管進(jìn)行焊接性試驗(yàn),在此基礎(chǔ)上進(jìn)行φ36×4,φ252×14垂直固定及水平固定位置的四項(xiàng)焊接工藝評(píng)定。焊接工藝評(píng)定宜在焊接試驗(yàn)室進(jìn)行。試驗(yàn)前擬定了與工程施工實(shí)際相同的焊接方案,評(píng)定原則、要求、方法均按ASME IX執(zhí)行。評(píng)定合格的工藝參數(shù)如下:
a、坡口條件
管壁厚(mm) 坡口形式坡口角度對(duì)口間隙(mm) 鈍邊(mm) 清理范圍(mm) ≤2 V 50° 0~0.8 0~0.8 每側(cè)50~100 <2 V 60° 0.5~2 1~1.5 每側(cè)50~100
b電源種類和特性直流正接
c焊接規(guī)范壁厚mm ≤2 3~4 4~7 6~7 >7 焊接層數(shù) 1 1~2 2~
3 3~4 4~5 鎢極直徑mm 2.0 2.0 2.0 3.0 3.0 焊絲直徑mm 2.0 3.0 3.0 3.0 3.0 焊槍直徑mm 10~12 16~20 16~20 16~20 16~
20 電壓V 10~12 12~14 12~14 12~14 12~14 電流A 40~70 80~
110 110~140 120~180 120~180 焊速cm/min 7.5~10 10~15 10~15 10~15 10~15 層間溫度℃ <200 <200 <200 <200 <200 線能量
KJ/cm 2.4~6.7 3.9~9.3 5.3~11.8 5.8~15.1 5.8~15.1 噴咀氬氣l/min 8
~12 12~15 15~20 15~20 15~20 保護(hù)罩氬氣l/min 16~25 2530 35~
45 35~45 35~45 管內(nèi)氬氣l/min 6~10 8~15 10~20 10~20 10~
20 氬氣保護(hù)時(shí)間S 30~60 >60 >60 >60 >60 保護(hù)區(qū)氬氣充裝系數(shù)
21.8 21.8 21.8 21.8 21.8
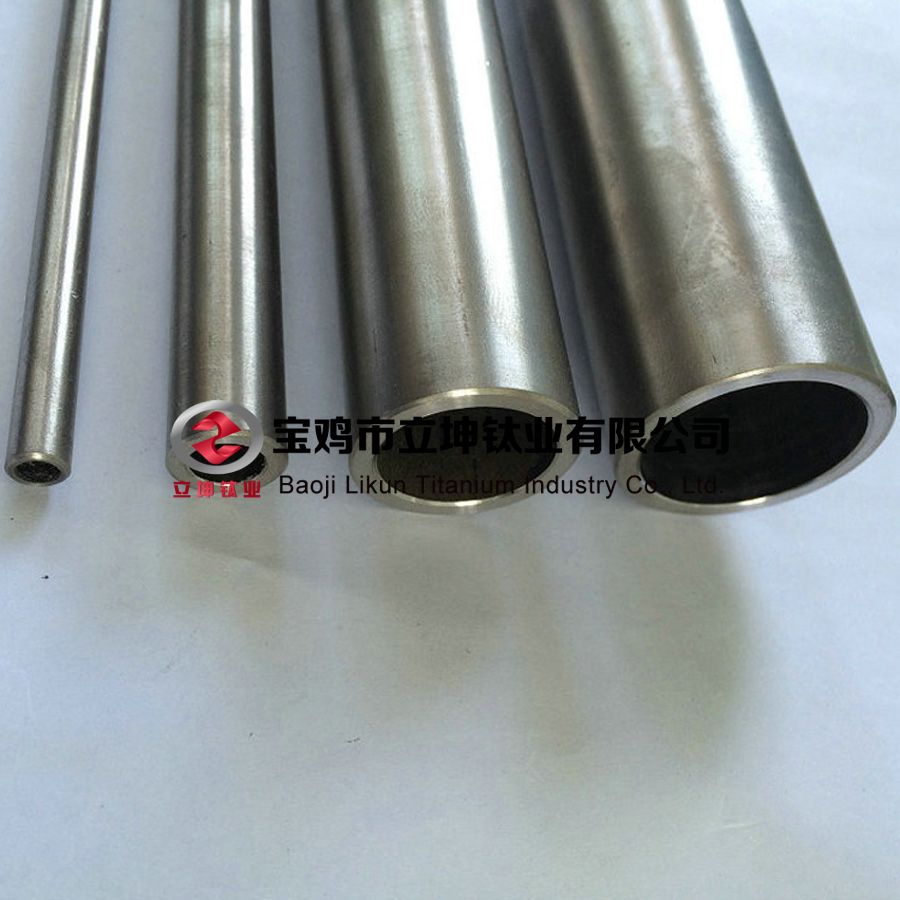
3.1.5.2 焊工資格
根據(jù)焊接工藝評(píng)定所提供的工藝參數(shù),在專家的指導(dǎo)下組織焊工進(jìn)行學(xué)習(xí),并請(qǐng)有經(jīng)驗(yàn)的焊工師傅作示范,對(duì)將參與焊接的焊工進(jìn)行操作技能培訓(xùn)和考試。結(jié)果參加培訓(xùn)的五名焊工全部通過(guò)DIN8560規(guī)定的考試,并參加鈦管的焊接工作。
3.1.5.3 焊材焊絲為德方提供的ERTi-2,規(guī)格經(jīng)工藝評(píng)定后確定為φ2.0、
φ3.0。焊絲在使用前應(yīng)按坡口的清理方法進(jìn)行表面清理及脫脂處理,施焊時(shí)焊絲的端部應(yīng)除去10~20mm長(zhǎng)。
3.1.5.4 焊接環(huán)境
鈦管施工需在預(yù)制廠房?jī)?nèi)進(jìn)行,在現(xiàn)場(chǎng)焊接固定口時(shí),應(yīng)根據(jù)需要搭設(shè)防雨、防風(fēng)棚,保證焊接環(huán)境符合工藝要求。若出現(xiàn)下列條件之一時(shí),不準(zhǔn)進(jìn)行焊接。
3.1.5.5 層間清理與保護(hù)
對(duì)多層焊道,在下一層施焊前,首先檢查表面氧化程度,如有異常情況,應(yīng)立即進(jìn)行表面處理或返修處理,處理時(shí)必須用專用的奧氏體不銹鋼制鋼絲刷和砂輪。
3.1.5.6 焊縫表面酸洗鈍化處理鈦材焊接后,經(jīng)表面色澤檢查合格后須對(duì)焊縫和熱影響區(qū)進(jìn)行酸洗鈍化處理。酸洗后必須立即用水徹底沖洗.以除去殘留在焊件上的酸液。整個(gè)酸洗過(guò)程的溫度應(yīng)控制在40℃以下。
酸洗鈍化液按下列比例 配方;
3.1.6 焊接檢驗(yàn)所有焊縫均應(yīng)進(jìn)行外觀檢查,X射線照相檢查,著色檢驗(yàn)和壓力試驗(yàn)等項(xiàng)檢驗(yàn),均應(yīng)合格。
相關(guān)鏈接