一、焊接方法的選擇
由于工業(yè)純鈦化學性能非?;顫?,與氧、氮、氬的親和力大,普通焊條電弧焊、氣焊及 CO2 氣體保護焊都不適用于鈦及鈦合金的焊接。我們選用手工鎢極氬弧焊進行鈦管道的焊接,利用焊槍噴嘴和內(nèi)、外氣體 保護托罩噴出的氬氣,把焊縫區(qū)和焊接熱影響區(qū)金屬與空氣隔開,以防止空氣侵入。
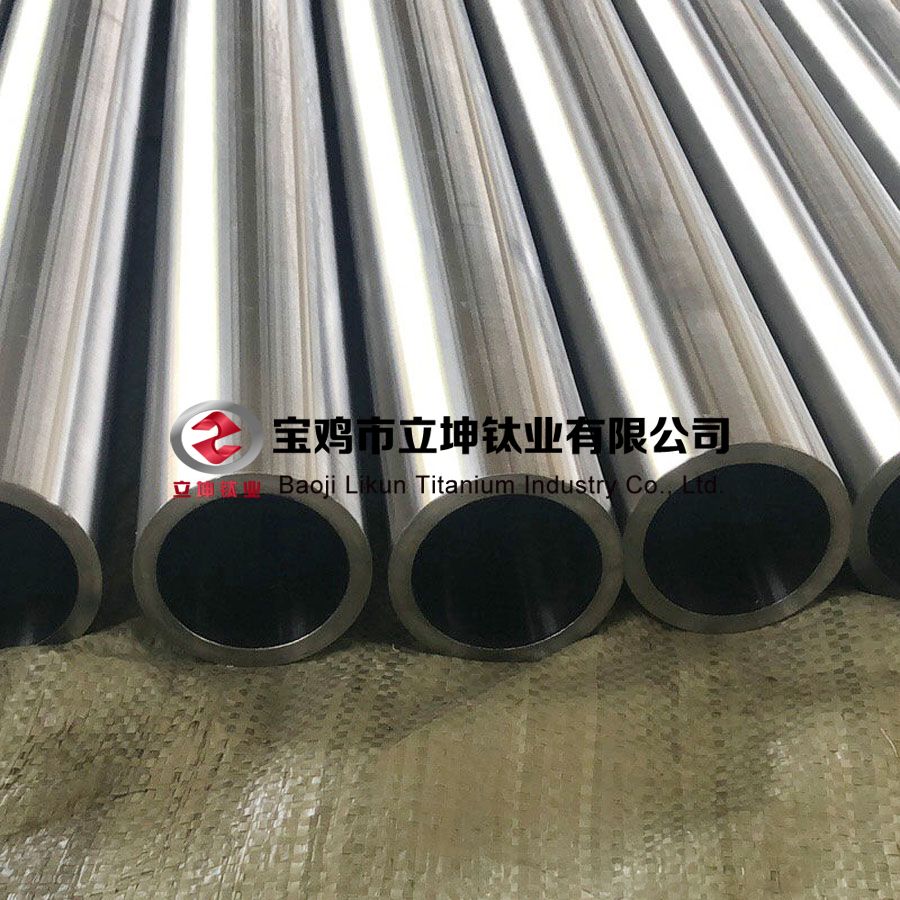
二、焊接材料的選擇
2. 1 填充焊絲的選用
鈦管道焊接用的焊絲成分應與母材金屬相同,其表面不得有燒皮、 裂紋、氧化色或金屬、非金屬夾雜物等缺陷存在;焊絲在焊接前應進行烘干。
2. 2 保護氣體的選用
鎢極氬弧焊時氬氣必須選用純度在≥99. 999%以上高純度氬氣。在大管徑鈦管道焊接過程中,由于要求連續(xù)充氣,中途不允許中斷停氣, 所以, 大管徑鈦管焊接時可采用純度高、容 暈大的液態(tài)氪氣 ( 1 瓶液氪相當千 30 余瓶氣態(tài)氪氣的容量)。每個液態(tài)氪氣瓶需做一個分氣缸, 分氣缸上安裝 4--5 個分氣嘴, 分別接上氬氣表, 一個液態(tài)氪氣瓶就可供4--5人同時焊接。液態(tài)氪氣使用裝置見圖1
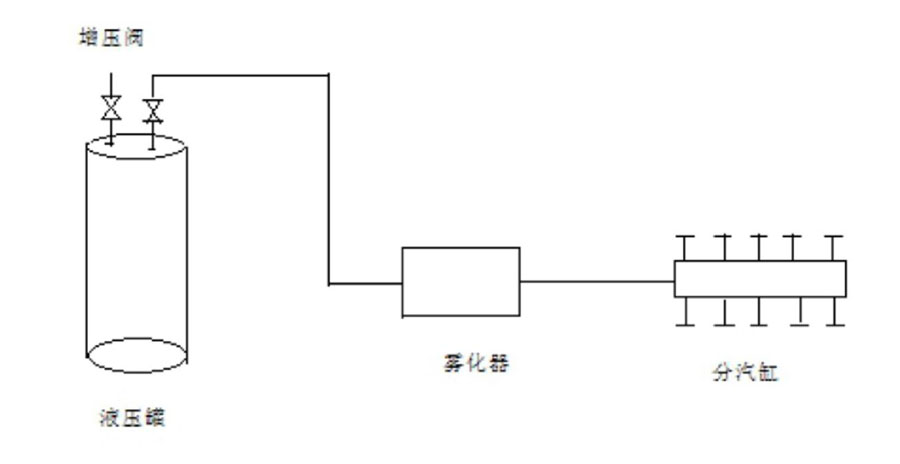
圖1 液化氬氣使用裝置示意圖
三、鈦管道坡口形式的選擇及坡口的清理
3.1坡口形式的選擇
在選擇鈦管道的焊接坡口形式時,應考慮盡最減少焊接層數(shù)和金屬填充量, 以降低焊縫的累積吸氣量, 防止焊接接頭塑性下降。紹興 30 萬噸/年 PTA 裝置 DN10000mm 鈦管道的厚度為 10.2mm , 我們選擇的坡口形式及尺寸見圖 2。
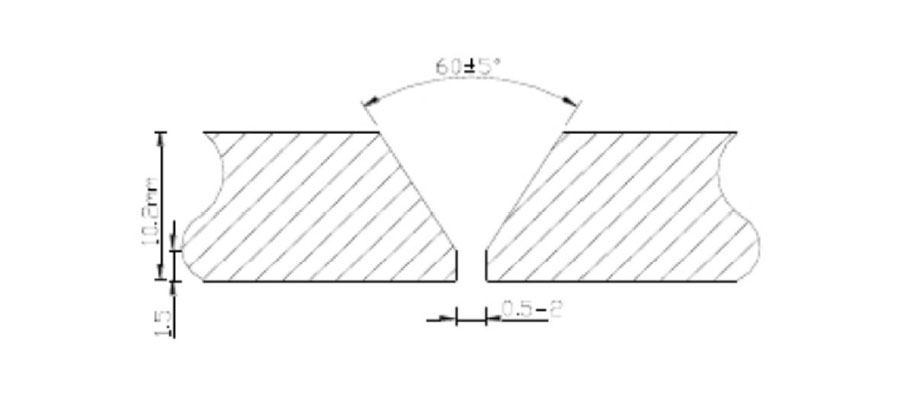
圖 2 焊接坡口形式及尺寸
3.2坡口的清理
鈦管道焊接前,應采用機械或化學清洗方法,對焊接坡口及其兩側(cè)各50mm 范圍內(nèi)的氧化皮、油脂和污染物等進行徹底清理。
a、機械清理
用不銹鋼絲刷或硬質(zhì)合金餃刀等機械方法對焊接坡口表面的氧 化膜進行清除,清理工具應專用并保持清潔,防止鐵污染等問題出現(xiàn)。
b、化學清洗
用酸洗溶液對焊接坡口進行酸洗,清除其表面的氧化膜,酸洗后, 用清水沖洗并用絲布擦干。酸洗后的焊接坡口表面應呈現(xiàn)銀白色。
3.3焊絲的清理
鈦管道焊接前,應采用機械或化學清洗方法,對焊接使用的鈦焊絲進行徹底的清理,鈦焊絲清理使用的方法和清理要求與坡口清理的方法和要求一致。
四、焊縫的組對和點固焊
4.1焊縫的組對
為了減少在鈦管道焊縫組對過程中鐵離子對已完成清理的坡口的污染, 保證焊口的組對質(zhì)量, 應特制專用的活動對口卡具進行輔助對口。這即可避免因在組對過程中使用鐵質(zhì)件而造成的鐵離子對焊接 坡口的污染;也可在焊口組對時通過調(diào)節(jié)絲杠,使管口保證同心,防 止對口錯邊現(xiàn)象的產(chǎn)生?;顒訉诳ň咭妶D 3。
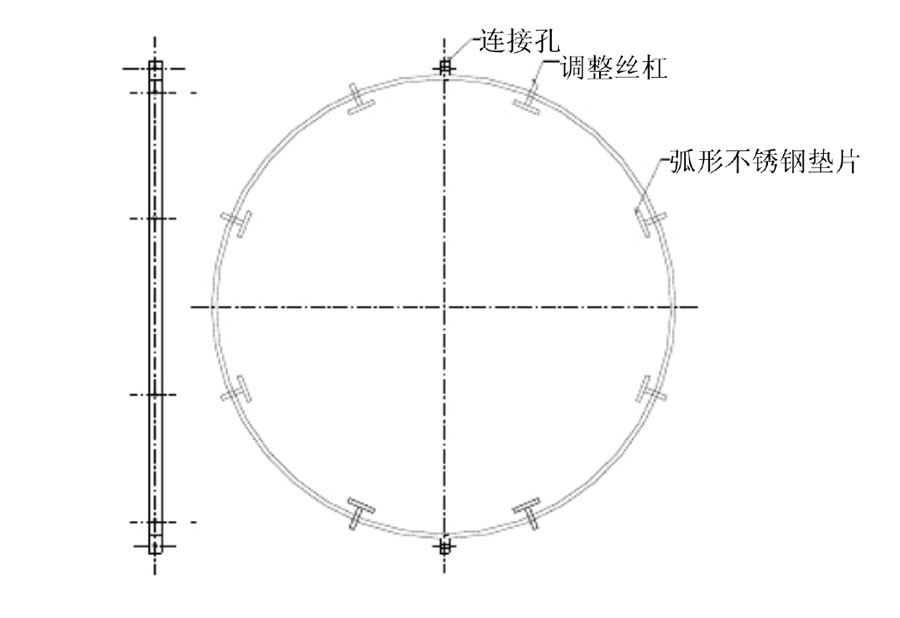
圖 3 活動對口卡具示意圖
4.2焊縫的點固焊
鈦管口組對點固焊點的間距應以100-150mm 為宜 ,點固焊點的長度以 10-15mm 為宜。點固焊所用的焊絲、焊接工藝參數(shù)及保護氣體等條件應與正式焊接相同。
五、焊接管口內(nèi)、外部氣體的置換和保護
5.1焊接管口內(nèi)部氣體的置換和保護
管口組對完成后, 應先進行管口內(nèi)部的氣體置換。對管徑DN1000的鈦管道,為加快氣體置換速度,降低氣體使用成本,且又能保證管口內(nèi)部氣體的置換質(zhì)量, 我們使用的氣體置換方式是: 人進入管道內(nèi)部, 手持一個內(nèi)部氣體保護托罩(內(nèi)部氣體保護托罩由輸氬管、不銹鋼絲網(wǎng)、拖罩外殼和手持銅管組成), 在開始焊接部位 , 形成一個與周圍空氣隔開的半封閉空間,然后通過放置在拖罩下部的輸氬管對氣體拖罩內(nèi)部進行充氬,進入拖罩的氬氣,通過不銹鋼絲網(wǎng)均勻地向氣體拖罩內(nèi)部的半封閉空間擴散,并逐漸將已封閉在氣體拖罩范圍內(nèi)的空氣完全排空,使處在氣體拖罩封閉范圍內(nèi)的高溫焊道及其熱影響區(qū), 在整個焊接過程中始終處于氬氣的充分保護之下,并持續(xù)到焊縫及熱影響區(qū)金屬冷卻到 200°C 以下。在焊接過程中, 人拿著內(nèi)部氣體保護托罩隨著外部的焊接電弧同步移動,使管道內(nèi)部的焊縫及熱影響區(qū)金屬始終處于氬氣的保護之下。內(nèi)保護操作示意圖見圖 4
在進行管道內(nèi)部氣體保護時,為了加快焊縫及熱影響區(qū)金屬的冷卻速度, 提高保護效果, 同時也為了加 快焊接速度, 焊接過程中盡量使用出口流量大、溫度低、儲存最大的液氪進行氣體保護和氣體置換。

圖 4 內(nèi)保護防護氣罩操作示意圖
5.2焊接管口外部氣體的置換和保護
由于鈦金屬具有的高溫化學活潑特性,在焊接過程中僅依靠氪弧焊 焊槍噴嘴噴射出的氬氣對熔池和高溫焊道及其熱影響區(qū)的保護,是無法保證焊接質(zhì)質(zhì)量的。為了增大鈦管焊接過程中的氬氣保護面積、延長氬氣保護時間, 保證焊接質(zhì)量, 必須特制管道外部氣體置換保護裝置, 對在高溫狀態(tài)下的焊接熔池和高溫焊道及其熱影響區(qū)進行焊接輔助保護。
我們使用外保護氣體托罩進行管口外部氣體保護。焊接管口外部保 護氣體拖罩由輸氬管、不銹鋼絲網(wǎng)、拖罩外殼、焊炬等構(gòu)成。焊接管口外部空氣置換過程與內(nèi)部氣體置換過程完全一致。常用的外保護氣體拖罩見圖 5。

圖 5 焊接管口外保護氣體拖罩示意圖
六、焊接管口內(nèi)、外部氣體的保護質(zhì) 量的檢測
焊接管口內(nèi)、外部托罩充氪置換工作完成后 , 應進行試焊, 通過觀察焊道色澤來判斷充氬置換和氣體保護的,只 有在確認充氪氬置換和氣體保護質(zhì)暈已經(jīng)達到合格要求后, 方可進行正式焊接。鈦焊道的色澤檢查表見表1。
焊縫和熱影響區(qū)的表面顏色表 1
焊縫級別 | 焊縫 | 熱影響區(qū) |
銀白、淡黃 | 深黃 | 金紫 | 深藍 | 銀白、淡黃 | 深黃 | 金紫 | 深藍 |
—級、二級、 三級 | 允許 | 不允許 | 不允許 | 不允許 | 允許 | 不允許 | 不允許 | 不允許 |
允許 | 允許 | 允許 | 允許 |
七、鈦管道焊接工藝參數(shù)的選擇
為了防止焊縫在高溫過熱區(qū)停留時間較長并避免焊后冷卻過程中 形成脆硬組織, 鈦管道焊接過程中應選用小規(guī)范進行焊接。鈦管的焊接工藝參數(shù)選擇見表 2。
鈦管焊接工藝參數(shù)表表 2
管徑 φ×δ | 1000×10.2 |
坡口形式 | V 型 |
鎢極直徑mm | 2. 5 |
噴嘴孔徑 mm | 25 |
氬氣流最 L. min | 主噴嘴 | 15- 20 / L. min |
外部拓罩 | 25- 35/ L. min |
內(nèi)部拓罩 | 30- 40/ L. min |
封底焊 | 焊絲直徑mm | 2. 0 |
電流 A | 90- 110 |
電壓v | 14- 15 |
焊接速度mm/ mi n | 8- 14 |
填充焊 | 焊絲直徑mm | 2. 4 |
電流 A | 100-120 |
電壓v | 14- 15 |
焊接速度mm/min | 8- 14 |
蓋面焊 | 焊絲直徑mm | 2. 4 |
申流A | 1 00- 120 |
電壓v | 14- 15 |
焊接速度mm/min | 8- 16 |
八、大管徑鈦管道的焊接要點
鈦管道的焊接施工, 必須編制焊接工藝卡并按照焊接工藝卡規(guī)定的焊接工藝進行施焊, 嚴格控制焊接線能量, 以減少焊接熱輸入, 縮短在焊縫高溫過熱區(qū)的停留時間, 防止形成脆硬組織和晶粒粗大現(xiàn)象的產(chǎn)生, 焊接層間溫度不得高千 200°C 。
焊接過程中必須制作并正確使用內(nèi)、外氣體保護拖罩, 以確保在焊接過程中對焊道、焊接熱影響區(qū)的保護質(zhì)量。為使焊接區(qū)域 處于良好的保護狀態(tài), 焊槍噴嘴直徑應選擇 20-25mm 為宜; 焊槍噴嘴噴出的氬氣應保持穩(wěn)定層流。
起弧時,焊槍必須提前送氣,并采用高頻引??;息弧時,應使用電 流衰減裝置和氣體保護裝置;焊接弧坑必須填滿;焊接時,粘貼在坡口 處的高溫膠帶應隨焊接隨揭開。
焊接過程中,填充焊絲的加熱端應始終處在氬氣的保護之下,息弧 后應在焊縫脫離氪氣保護時方可取出;焊絲如被污染或氧化變色時,其 污染或氧化變色部分應予清除。
焊接過程中應注意觀察焊道色澤,以確認氣體保護效果和焊接質(zhì) 量。如在焊接過程中發(fā)現(xiàn)有明顯的焊縫氧化現(xiàn)象時, 應立即停止焊接, 待查明原因并實施糾正處置后才能繼續(xù)焊接。
現(xiàn)場施焊時,必須采取防風措施,以防環(huán)境風對焊接保護區(qū)的影響, 確保氬弧氣體的焊接保護效果。
相關(guān)鏈接